Omni
New Member
Enough with the lurking for me, it is time for my first build!
I first took notice of the RPF because I had heard Adam Savage mention it - because really, everything he does is cool. I quickly found a build that I got excited about - Evil Dead II/Army of Darkness replica chainsaw. jimmydellamorte and the others that contributed to the thread did such an amazing job on their saws I setup a Google alert for Homelite in my area. A few months ago I picked up a Homelite 2 Super and I am now ready to give it a new life.
I will be using many of the great ideas I have seen here and I hope to credit them along the way. I intend to contribute to the community by providing as much detail as I can for the things I end up winging in case others are curious. I also have a surprise 'feature' planed for the finish (as a hint it is not an interactive element
.
START:
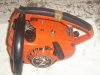
The body of the saw is not the same model as the one in the movie but I could find little to no difference in the exterior details for the exception of the stock handle. This doesn't pose much of a problem though because it is the first thing to cut off!
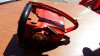
I lost the pictures of taking the saw apart but they really aren't required for someone that wants to do this. Just a basic socket set and screwdriver will do the trick. The case is held together with four bolts, then a number of screws seen from the outside hold the engine inside.
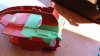
Once I had the casing empty I masked off where I was going to cut so I could draw some cut lines. I opted to cut as little off as possible.
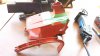
I picked up a Dremel Saw-Max that made very short work of cutting through the case. Because of the size of the tool I roughly cut the handle off so I could do nice clean cuts where it counts.
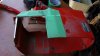
For where to cut I tried to follow the natural lines where the handle attached to the case.
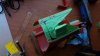
On the hand port side I measured 1cm in from the left side, 1cm from the top and flush with the bottom of the case.
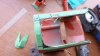
The straight cuts were made with the Dremel Saw-Max, the rounded cuts were done with a standard Dremel and a cut-off wheel. After this cut was done I realized that the hole was not going to be tall enough for my wrist to be vertical. Getting the tools back out I got rid of the top 2cm lip to match the bottom, this gives enough room to turn my wrist upright in the opening.
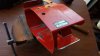
To be more accurate I ground off most of the top lip but left some of the original height on the right. If I were to do this again I would remove only what I need to on the top lip as I feel I will need to fill in that area later so the hole isn't so obvious.
Cost : $15 for Saw
Time: 1 hour
More tomorrow!
I first took notice of the RPF because I had heard Adam Savage mention it - because really, everything he does is cool. I quickly found a build that I got excited about - Evil Dead II/Army of Darkness replica chainsaw. jimmydellamorte and the others that contributed to the thread did such an amazing job on their saws I setup a Google alert for Homelite in my area. A few months ago I picked up a Homelite 2 Super and I am now ready to give it a new life.
I will be using many of the great ideas I have seen here and I hope to credit them along the way. I intend to contribute to the community by providing as much detail as I can for the things I end up winging in case others are curious. I also have a surprise 'feature' planed for the finish (as a hint it is not an interactive element
START:
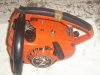
The body of the saw is not the same model as the one in the movie but I could find little to no difference in the exterior details for the exception of the stock handle. This doesn't pose much of a problem though because it is the first thing to cut off!
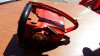
I lost the pictures of taking the saw apart but they really aren't required for someone that wants to do this. Just a basic socket set and screwdriver will do the trick. The case is held together with four bolts, then a number of screws seen from the outside hold the engine inside.
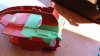
Once I had the casing empty I masked off where I was going to cut so I could draw some cut lines. I opted to cut as little off as possible.
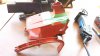
I picked up a Dremel Saw-Max that made very short work of cutting through the case. Because of the size of the tool I roughly cut the handle off so I could do nice clean cuts where it counts.
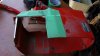
For where to cut I tried to follow the natural lines where the handle attached to the case.
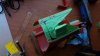
On the hand port side I measured 1cm in from the left side, 1cm from the top and flush with the bottom of the case.
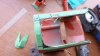
The straight cuts were made with the Dremel Saw-Max, the rounded cuts were done with a standard Dremel and a cut-off wheel. After this cut was done I realized that the hole was not going to be tall enough for my wrist to be vertical. Getting the tools back out I got rid of the top 2cm lip to match the bottom, this gives enough room to turn my wrist upright in the opening.
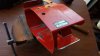
To be more accurate I ground off most of the top lip but left some of the original height on the right. If I were to do this again I would remove only what I need to on the top lip as I feel I will need to fill in that area later so the hole isn't so obvious.
Cost : $15 for Saw
Time: 1 hour
More tomorrow!
Last edited: