brutuswayne
Active Member
Re: Captain American Civil War Build (Overshirt Complete, Next: Pants
Pants are done! This post is gonna be a big one since I basically sped through 60% of the construction since my last post. But now I'm about where I should be schedule-wise so I can relax a slight amount as I begin the remaining accessories.
Up first was making the panels at the back of the knee and setting them in. This was probably the hardest to find references of and I had to use a mix of slightly out of focus side shots from the set, and shots of the toy replica to figure out the shape. I think I ultimately got it right though, or at least close enough for a detail that's not immediately visible. After that was all embossed, I also made the remaining bottom half of the leg and the one pentagon-ish shaped panel and attached all of that to the existing pants legs.
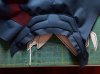
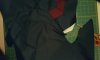
Next was my least favorite part of making Cap pants, the kneepads. I already had a pretty good pattern, but it took me a while to sew as I figured out the best construction order. Ultimately what I did was sew together the individual panels, then emboss them like that, and finally fold/pin the excess, which was then pinned onto the jumbo spandex base and topstitched in place. This ended up being the most precise and efficient method for me, despite still taking a while. The same process was used for the bigger section of the kneepad.
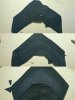
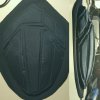
After the kneepads were fully constructed, I set them into the pants by folding/pinning the edges of the pants panels, lining them up with the seam lines of the kneepads, and pinning those in place. Think of it like the same way I did the actual kneepads cordura sections. I had previously marked the seamlines on the face side of the spandex by basting along the chalk line on the back side. Once the kneepads were pinned in place and top-stitched down, I carefully removed the basted stitch.
Next I had to close up the pant leg which presented an interesting challenge. The way I patterned the pants, the section at the abck of knee wrapped all the way around from the sides of the kneepad with no break. But, the regular side seams of the pants still existed. This created an interesting problem where I had to sew the exposed part of the knee-back panels, into the gap in the other side of the pants. If it sounds confusing, that's because it was. You can see how I eventually managed to sew it all in place and topstitch it to secure, but it's a bit messier than a lot of my other seams. Thankfully, it's also the least visible area as it's on the inside of the pant legs. Aaaand then just for funsies, I pinned the first completed leg to my mannequin to check how everything lined up and looked.
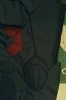
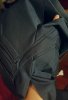
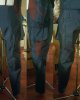
Home-stretch. After constructing both legs, I added the zipper. I have a kind of unorthodox method for installing zippers that comes from the fact I don't actually know how to do it properly. But, after wrestling a bit I was able to get it into the fly, and I think it actually came out better than the zipper on my AoU pants! I also made a liner for the pants using leftover jumbo spandex and ponte from previous projects, just so that I didn't have to wear leggings underneath again. Cordura is very scratchy against bareflesh, especially thighs. After finishing the liner, I realized that I needed to undo the topstitching at the zipper panels to slide the liner behind them though. This is because the liners go all the way up to the fly seam, but that would also cover one side of the zipper as is. So I popped open those seams, inserted the liner, and quickly topstitched them back up (those seams actually ended up even cleaner than the ones in the photo below).
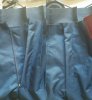
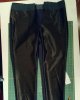
Last steps not worth documenting, hemming the waistband and cuffs with simple topstitching, and adding snaps to connect the pants to the undershirt. So I'll just end it with a few shots of the pants laid out on my table, and a picture of me wearing the suit so far testing it for...mobility. Yeah, that's what I'm doing.
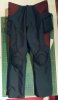
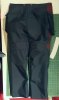
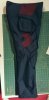
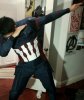
Pants are done! This post is gonna be a big one since I basically sped through 60% of the construction since my last post. But now I'm about where I should be schedule-wise so I can relax a slight amount as I begin the remaining accessories.
Up first was making the panels at the back of the knee and setting them in. This was probably the hardest to find references of and I had to use a mix of slightly out of focus side shots from the set, and shots of the toy replica to figure out the shape. I think I ultimately got it right though, or at least close enough for a detail that's not immediately visible. After that was all embossed, I also made the remaining bottom half of the leg and the one pentagon-ish shaped panel and attached all of that to the existing pants legs.
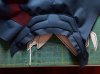
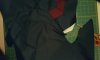
Next was my least favorite part of making Cap pants, the kneepads. I already had a pretty good pattern, but it took me a while to sew as I figured out the best construction order. Ultimately what I did was sew together the individual panels, then emboss them like that, and finally fold/pin the excess, which was then pinned onto the jumbo spandex base and topstitched in place. This ended up being the most precise and efficient method for me, despite still taking a while. The same process was used for the bigger section of the kneepad.
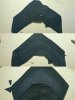
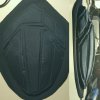
After the kneepads were fully constructed, I set them into the pants by folding/pinning the edges of the pants panels, lining them up with the seam lines of the kneepads, and pinning those in place. Think of it like the same way I did the actual kneepads cordura sections. I had previously marked the seamlines on the face side of the spandex by basting along the chalk line on the back side. Once the kneepads were pinned in place and top-stitched down, I carefully removed the basted stitch.
Next I had to close up the pant leg which presented an interesting challenge. The way I patterned the pants, the section at the abck of knee wrapped all the way around from the sides of the kneepad with no break. But, the regular side seams of the pants still existed. This created an interesting problem where I had to sew the exposed part of the knee-back panels, into the gap in the other side of the pants. If it sounds confusing, that's because it was. You can see how I eventually managed to sew it all in place and topstitch it to secure, but it's a bit messier than a lot of my other seams. Thankfully, it's also the least visible area as it's on the inside of the pant legs. Aaaand then just for funsies, I pinned the first completed leg to my mannequin to check how everything lined up and looked.
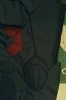
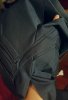
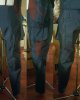
Home-stretch. After constructing both legs, I added the zipper. I have a kind of unorthodox method for installing zippers that comes from the fact I don't actually know how to do it properly. But, after wrestling a bit I was able to get it into the fly, and I think it actually came out better than the zipper on my AoU pants! I also made a liner for the pants using leftover jumbo spandex and ponte from previous projects, just so that I didn't have to wear leggings underneath again. Cordura is very scratchy against bareflesh, especially thighs. After finishing the liner, I realized that I needed to undo the topstitching at the zipper panels to slide the liner behind them though. This is because the liners go all the way up to the fly seam, but that would also cover one side of the zipper as is. So I popped open those seams, inserted the liner, and quickly topstitched them back up (those seams actually ended up even cleaner than the ones in the photo below).
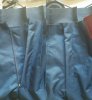
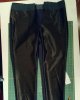
Last steps not worth documenting, hemming the waistband and cuffs with simple topstitching, and adding snaps to connect the pants to the undershirt. So I'll just end it with a few shots of the pants laid out on my table, and a picture of me wearing the suit so far testing it for...mobility. Yeah, that's what I'm doing.
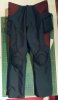
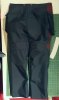
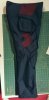
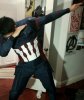
Last edited: