BOOTS
So, as it happens, I also made boots. From scratch.
Yup.
First thing I did was went out and bought a pair of lasts. A last is essentially a wooden shoe mold, upon which you make your shoe. Their is a last for the right foot, and a last for the left foot. Lasts last, lastly, largely until they lack luster. If that made any sense, I commend you on your imagination.
Anyway, I tacked a piece of leather to the bottom of the last and began to form the inner sole.
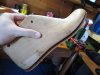
Next I used a pattern to cut out the basic boot pieces. I dyed them and stitched them together.
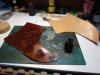
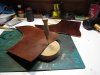
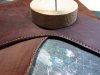

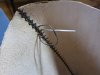
Again everything had to be hand stitched. Used the awl (second from the left) to punch all the holes, and then stitched the pieces together. I had to kind of improvise on the stitching technique, using a variation of the regular double needle stitch. Passing the thread through once didn't seem strong enough, so I figured passing it through would work. It has so far.
Once the basic boot "uppers" as they're called were finished, the fun began. I placed it over the last and began "turning" it. I used a pliers to grab the leather in various sections, working my way back and forth around the last, folding the leather over, and briefly holding it in place, taught, while securing it with tacks.
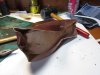
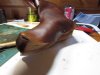

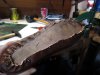
Once it was held down all around, I gently lifted the leather up enough to smear generous amounts of contact cement in between the turned upper and the insole. I used a hammer to press the leather down while the cement hardened. I also used a mallet to whack the entire shoe, everywhere, all over, to help persuade the leather to keep its shape once I removed the last.
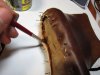
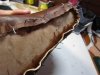
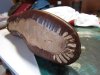
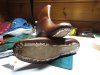
The next step was to attach the welt, which is a spiked, cross-sectionally triangular piece that helps ease the transition between the outer sole and the upper, since the sole is flat while the upper is round. This piece was secured with contact cement and given a hearty bashing to help ensure it stays stuck like its supposed to.
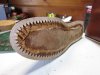
Then the welt was secured, and I had filed the leather a bit to promote traction, and ensure the cement holds, I prepared to the outer soles by cutting out two pieces of thick, extremely hard leather. I scratched them up again to help with bonding, and glued them to the bottom of the shoe. Again, they were hammered excessively.
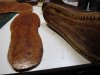
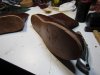
I used a knife, a piece of glass, sandpaper, and a rotary tool to help me smooth out the edge of the sole. I still didn't get a perfect shape, but that thick leather was torture to cut. Half the time I was terrified I would slip and mess up my shoe... the other half of the time I was terrified I would slip and cut off a finger or something worse. This leather is RIDICULOUS to cut.
In any case, after this ordeal, I took the shoe to cobbler to add the final rubber sole underneath (at this point I was struggling to finish the rest of the suit, and didn't have time to do it myself, although I'm sure I could have). The side of the sole was varnished, and the shoe was essentially done. At this point I began work on the upper parts of the boot.
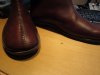