Hydrargyros
New Member
Hello all! This is my first build. I haven't been working on it for very long, but I have a lot of plans thought out. I will show you what I have at the moment, just to give an idea of what I am planning, how it works, and where I will take it - although I am fairly set on restarting from scratch (I will explain more at the end). For people who haven't seen the musical, the Little Shop of Horrors is a movie musical about a man-eating plant from space. I've seen a few Audrey II props before, almost all of which were sculpted/formed/etc. and painted. There was one that I've seen (https://www.youtube.com/watch?v=i2OaRzZxKJQ, by Ashton McCarthy-Gould on Youtube) that is animatronic and remote-controlled, which has served as a good reference point for me, although I am doing things a lot differently, for reasons I will outline briefly later on.
So, to get started, my considerations when planning out the mechanics. Primarily, I wanted a realistic range of movements. The plant used in the film (see https://www.youtube.com/watch?v=5ea5jKFGgUw) was a puppet (and, trivia time, was actually recorded at half speed - so Rick Moranis had to act and speak some of his scenes at half speed too!), so I knew I had a difficult task ahead of me. This initially meant a lot of servos, but over a few iterations of designs I managed to cut back to 8 servos (although this later became 9, with the extra being a duplicate due to wanting a second to control and balance the jaw opening and closing).
What I have so far: a basic balsa wood frame for the upper and lower parts of the head. At their bases, they are 170mm long by 140mm wide, which won't be the final dimensions because of how I plan to skin Audrey. I've cut holes for servos to go in - the white 9g servo near the front will have a metal arm controlling the lip, while the black 30g (along with a partner which is on the opposite side, not included in these pictures) are for opening and closing the lower jaw. The final photo shows (roughly) the largest angle of opening of the mouth. Apologies for poor photo quality, all I really have at the minute is my phone.
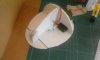
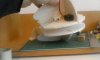
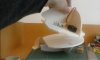
They will be hinged at the back using a standard hinge I picked up at a hardware shop for about £1.50. The blocks of beech you can see in the top right of picture 1 fit at the back of the jaws, and are for me to screw that hinge into. However, I plan to re-do this all, by 3D printing it. It feels a bit silly making this post when the only part of it I have actually completed is the part that I plan to re-do, but I have good reason: I want to 3D print the frame, because I'm not completely satisfied with the structural stability of the balsa wood frame. I want to screw the servos in place, and I would have to make it quite elaborate and hard to reproduce with a mixture of beech parts. Also, I am honestly slightly worried about the potential for fire, even though I know it's low risk. Additionally, it will make it a lot easier for me to plan the other parts (which I will have to 3D print anyway, more on that in a bit) if I have everything in CAD. And, finally, I have to admit that I forgot to account for the servo that will control the tongue when cutting out the lower part of the head.
The 'neck' of the plant (not the stem/stalk! The neck, as I define it here, is at the top of the stem) controls the rotations of the head. One servo's horn will be attached to the plate at the back of the top half of the head, to control the yaw (clockwise/anticlockwise when looking at the head from the front), and another will control the forwards/backwards tilt. The tilt/yaw planes of rotation seemed more important than pan/tilt, given the movement that the plant has in the film. The next part is the stalk itself - again, in my quest for realistic movement, I decided to go with (for lack of knowledge of a more descriptive/technical name) a flexible tube with wires running through holes at the side (see this video for an idea: https://www.youtube.com/watch?v=EVHtCP6BhjA). Using a pair of servos stored in the flowerpot at the base (one for forward/backward, one for left/right), the wires would give a smooth bend along the entire stalk. My plan is to 3D print these parts: a hollow center tube in ninjaflex, so that wires from the servos in the head and heck have somewhere to run down to a servo driver in the base), and a series of ABS rings which I would chemically weld along the stalk.
What's left is the skinning - I plan to use polyurethane foam sheets of about 10mm thickness, so that they are flexible (important for the neck and lips), and have a relatively spongey feel to the touch instead of being rigid. I plan to skin this using layers of coloured silicon (inspiration from this video: https://www.youtube.com/watch?v=rBNCvOILwmc). I chose silicone over latex because of what he says in that video - latex can get sticky, and gets hard to clean, and after a year or two it begins to degrade. Now, one question I do have is: what sort of lifetime would this silicone have? As I am going for maximum lifespan, would I be better off using silicone (from a tube for caulking tiles, as the guy in the video does), or latex with isoflex to protect it?
So, that's all for now - I plan to update once I have made some progress in drawing the parts up in CAD, which shouldn't be too long - the wait will mainly come in the form of trying to find somewhere to print the parts. I hope you like what you see so far, stay tuned!
So, to get started, my considerations when planning out the mechanics. Primarily, I wanted a realistic range of movements. The plant used in the film (see https://www.youtube.com/watch?v=5ea5jKFGgUw) was a puppet (and, trivia time, was actually recorded at half speed - so Rick Moranis had to act and speak some of his scenes at half speed too!), so I knew I had a difficult task ahead of me. This initially meant a lot of servos, but over a few iterations of designs I managed to cut back to 8 servos (although this later became 9, with the extra being a duplicate due to wanting a second to control and balance the jaw opening and closing).
What I have so far: a basic balsa wood frame for the upper and lower parts of the head. At their bases, they are 170mm long by 140mm wide, which won't be the final dimensions because of how I plan to skin Audrey. I've cut holes for servos to go in - the white 9g servo near the front will have a metal arm controlling the lip, while the black 30g (along with a partner which is on the opposite side, not included in these pictures) are for opening and closing the lower jaw. The final photo shows (roughly) the largest angle of opening of the mouth. Apologies for poor photo quality, all I really have at the minute is my phone.
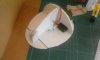
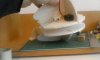
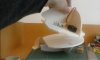
They will be hinged at the back using a standard hinge I picked up at a hardware shop for about £1.50. The blocks of beech you can see in the top right of picture 1 fit at the back of the jaws, and are for me to screw that hinge into. However, I plan to re-do this all, by 3D printing it. It feels a bit silly making this post when the only part of it I have actually completed is the part that I plan to re-do, but I have good reason: I want to 3D print the frame, because I'm not completely satisfied with the structural stability of the balsa wood frame. I want to screw the servos in place, and I would have to make it quite elaborate and hard to reproduce with a mixture of beech parts. Also, I am honestly slightly worried about the potential for fire, even though I know it's low risk. Additionally, it will make it a lot easier for me to plan the other parts (which I will have to 3D print anyway, more on that in a bit) if I have everything in CAD. And, finally, I have to admit that I forgot to account for the servo that will control the tongue when cutting out the lower part of the head.
The 'neck' of the plant (not the stem/stalk! The neck, as I define it here, is at the top of the stem) controls the rotations of the head. One servo's horn will be attached to the plate at the back of the top half of the head, to control the yaw (clockwise/anticlockwise when looking at the head from the front), and another will control the forwards/backwards tilt. The tilt/yaw planes of rotation seemed more important than pan/tilt, given the movement that the plant has in the film. The next part is the stalk itself - again, in my quest for realistic movement, I decided to go with (for lack of knowledge of a more descriptive/technical name) a flexible tube with wires running through holes at the side (see this video for an idea: https://www.youtube.com/watch?v=EVHtCP6BhjA). Using a pair of servos stored in the flowerpot at the base (one for forward/backward, one for left/right), the wires would give a smooth bend along the entire stalk. My plan is to 3D print these parts: a hollow center tube in ninjaflex, so that wires from the servos in the head and heck have somewhere to run down to a servo driver in the base), and a series of ABS rings which I would chemically weld along the stalk.
What's left is the skinning - I plan to use polyurethane foam sheets of about 10mm thickness, so that they are flexible (important for the neck and lips), and have a relatively spongey feel to the touch instead of being rigid. I plan to skin this using layers of coloured silicon (inspiration from this video: https://www.youtube.com/watch?v=rBNCvOILwmc). I chose silicone over latex because of what he says in that video - latex can get sticky, and gets hard to clean, and after a year or two it begins to degrade. Now, one question I do have is: what sort of lifetime would this silicone have? As I am going for maximum lifespan, would I be better off using silicone (from a tube for caulking tiles, as the guy in the video does), or latex with isoflex to protect it?
So, that's all for now - I plan to update once I have made some progress in drawing the parts up in CAD, which shouldn't be too long - the wait will mainly come in the form of trying to find somewhere to print the parts. I hope you like what you see so far, stay tuned!