I am finally able to see a dream come true with all the new technology available to allow something at this scale to happen a reasonable cost in time invested and material. My hats are off to all the purists/artists who have created masterpieces by collecting all the required kits needed to bring those spectacular models to fruition. I am late to the game unfortunately and don't want to turn this into a 16 year long crusade like my R2 unit or a similar length build for both my life-size Stormtrooper and Boba Fett displays. I have began by putting a criteria on minimal investment for the maximum detail and least amount of weight possible. To that end I will be 3D printing in both FDM and resin formats. The frame is starting with an 8"x10" 6mm Birch drum shell with 1/2" Baltic Birch top/bottom along with Baltic Birch plywood frame members. The subframe is 2"aluminum airline piping for both horizontal and vertical mounting. The components for the completed shell currently weight in at 26 pounds total including the 3D printed shell. I have just started to complete the assembly in Solidworks in the attached files. The 3D printing aspect will be new to me from an FDM standpoint so I look forward to feedback from the members as to how rigid PLA is as a material and if extra reinforcement may be necessary. I am 57 now and hope to have this completed by my retirement but all the best laid plans can get sidetracked at any time. Hopefully I can stay the course and have something that both I can be proud of and be able to share with my kids and grandkids and our love for Star Wars and its most iconic ship.
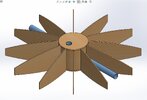
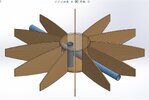
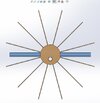
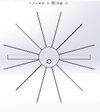
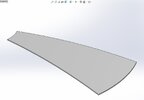
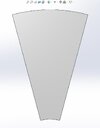
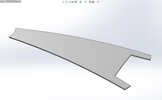
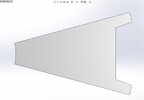
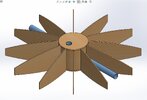
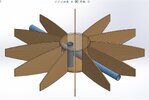
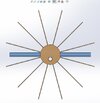
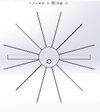
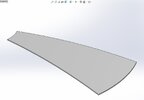
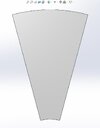
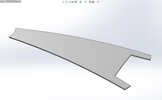
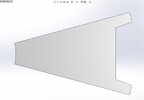
Last edited: