Gombabomb
Active Member
Hi again! First off... apologies if this thread isn't in the right spot. Not so sure if it would be considered more of a prop or a model.
A while back, designed and made a miniature naval mine which was probably my first 3D designed/printed object without print issues and was actually completely finished. Resembled a mace/flail head more than a mine in the end but since it had turned out well it gave me the motivation to design a new one from scratch that was closer in appearance to a real sea mine. The improved version is a little under 4" diameter including the pins:
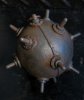

The original resides on my shelf but I had a few slots for made-to-order ones open and a couple months ago someone contacted me inquiring if a larger one somewhere around 7" diameter (not including pins) would be possible. Had an early April deadline so other projects took precedence but now that the mini nuke project is on hold for lack of mold materials and the deadline coming up, started to really make progress on the mine.
Originally attempted a 12" diameter build with a large green foam sphere and cast resin pins from a printed prototype I modeled with elements of German and Russian naval mines after trawling the internet for reference photos:
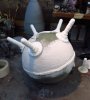
After casting and attaching the pins they were definitely too large for the sphere which was acquired later. Not sure why I didn't notice until after I had cast all 10 of them. :confused Also couldn't find anything suitable to harden the foam that wouldn't crack and flake with impact or rough handing so this attempt was scrapped.
Decided to go back to the way the earlier versions were made but had to scale it back down to a 7" diameter sphere since the printer's build plate is only a little more than 7" in one direction. Used the model for the pins designed for the 12" mine and rescaled and changed them a little to bring them into a more realistic proportion with the 7" sphere.

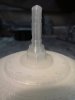

Both hemispheres of the new mine printed without much issue, each taking about 3 hours. The pins were about 10 minutes apiece when printed individually but took about 40 for groups of 5 (plate leveling/startup/warmup for single small objects takes more time than you'd expect).


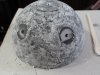

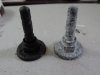
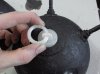
After very light sanding (found a way to make higher resolution polygons/spheres) both halves were primed then base coated with acrylics before the rust texture was applied with modeling paste. Worked on the halves while waiting for the sets of pins to print. Pins were primed, base coated, and then textured the same way. The anchoring ring pin parts were printed last. The ring will be glued together inside the hoop once painted and then touched up at the seam.

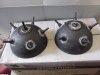

After affixing the pins with a solvent-based glue, more modeling paste was added to build up excess rust texture. After the last coat of primer the texture is a little more visible. Now that the primer's good and dried the flat dark gray coat is next followed by the rust and weathering, by far the most satisfying step.
More photos as it progresses. : )
How is it looking so far?
A while back, designed and made a miniature naval mine which was probably my first 3D designed/printed object without print issues and was actually completely finished. Resembled a mace/flail head more than a mine in the end but since it had turned out well it gave me the motivation to design a new one from scratch that was closer in appearance to a real sea mine. The improved version is a little under 4" diameter including the pins:
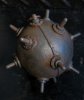

The original resides on my shelf but I had a few slots for made-to-order ones open and a couple months ago someone contacted me inquiring if a larger one somewhere around 7" diameter (not including pins) would be possible. Had an early April deadline so other projects took precedence but now that the mini nuke project is on hold for lack of mold materials and the deadline coming up, started to really make progress on the mine.
Originally attempted a 12" diameter build with a large green foam sphere and cast resin pins from a printed prototype I modeled with elements of German and Russian naval mines after trawling the internet for reference photos:
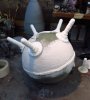
After casting and attaching the pins they were definitely too large for the sphere which was acquired later. Not sure why I didn't notice until after I had cast all 10 of them. :confused Also couldn't find anything suitable to harden the foam that wouldn't crack and flake with impact or rough handing so this attempt was scrapped.
Decided to go back to the way the earlier versions were made but had to scale it back down to a 7" diameter sphere since the printer's build plate is only a little more than 7" in one direction. Used the model for the pins designed for the 12" mine and rescaled and changed them a little to bring them into a more realistic proportion with the 7" sphere.

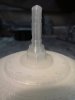

Both hemispheres of the new mine printed without much issue, each taking about 3 hours. The pins were about 10 minutes apiece when printed individually but took about 40 for groups of 5 (plate leveling/startup/warmup for single small objects takes more time than you'd expect).


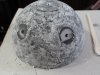

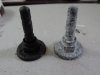
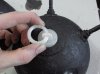
After very light sanding (found a way to make higher resolution polygons/spheres) both halves were primed then base coated with acrylics before the rust texture was applied with modeling paste. Worked on the halves while waiting for the sets of pins to print. Pins were primed, base coated, and then textured the same way. The anchoring ring pin parts were printed last. The ring will be glued together inside the hoop once painted and then touched up at the seam.

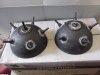

After affixing the pins with a solvent-based glue, more modeling paste was added to build up excess rust texture. After the last coat of primer the texture is a little more visible. Now that the primer's good and dried the flat dark gray coat is next followed by the rust and weathering, by far the most satisfying step.
More photos as it progresses. : )
How is it looking so far?
Last edited: