Probably something like this, just not as extreme in height...
https://www.youtube.com/watch?v=VbaQLlbMvjI
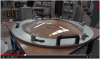
(I'd need to crack open my Mechanics Of Materials book from engineering school and see what the math says about the resultant shape of a blown "homogeneous" heated material of "constant" thickness under a pressure load...I bet the resultant shape would be mostly spherical...mostly)
ab
https://www.youtube.com/watch?v=VbaQLlbMvjI
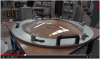
(I'd need to crack open my Mechanics Of Materials book from engineering school and see what the math says about the resultant shape of a blown "homogeneous" heated material of "constant" thickness under a pressure load...I bet the resultant shape would be mostly spherical...mostly)
ab
Last edited: