Re: John Long Phaser 1 Kit Buildup plus MM P2 Restoration
My
Axanar blog piece is in, so here I am with the latest on yesterday's debacle/triumph/porn shoot (one of those may not be entirely factual).
I got into the shop yesterday full of hope and cheese. Seriously, I ate a lot of cheese yesterday.
I broke out my
1/4" brass bar from Online Metals, and took it into the machine shop for the usual marking up with the height gage. At 1" x 6", it only comes to $7.
I followed the technique I saw on YouTube by
Tubalcain on how to mark holes with a height gage. It's definitely worth a look, and I've gotten great results with it.
I finally got to try out my machinist's punch, too -- it's excellent for punching machinists, but yesterday I just stuck to the brass.
You just drag it along the grooves you make with the height gage till you feel it nestle into the spot where they intersect, and give it a thunk. Like buttah.
You can also use a regular center punch and a mallet, but that's one more tool than I can use at a time without mashing my middle finger, and I need that to drive.
Next up, time to set the belts on the drill press. Because God forbid they should put a knob on these things.
The chart says 3,000 rpm for brass up to 3/16", so I set the belts for what I hoped was 2950, but really, how can you tell? The damn thing's Chinese, and 2950 is probably Mandarin for "Warp Eleventy-Five."
Not shown: Ludicrous Speed.
So, Tubalcain recommends not clamping down your work when you have a punched center like this. Instead, he says to just guide the work with your hand, and gently drop the drill bit into the work, letting the bit wobble its way into the punch. And I'll be damned, that works really well!
Of course, what Tubalcain doesn't tell you is that at Techshop, you better damn well wear ear protection at the drill press, because chances are some shmuck will be ten feet away from you on the Water Jet.
Actual shmuck may differ from picture.
If you've never heard a Water Jet, try to imagine watching
Star Trek Into Darkness with a xenomorph who hates J.J. Abrams even more than you do. I've heard less eardrum-ripping screeches from a toddler on a hotplate. You probably shouldn't try that at home.
Tubalcain also fails to mention how hot it can get in there when the AC is on the fritz. (Seriously, why do I watch that old fart's videos anyway?) But that's when you reach for ASA Law's patented man-portable air conditioner, which the other shop denizens insist on calling the "compressed air nozzle."
If this lawyer thing doesn't work
out, maybe I can rent myself out
as a putting green.
So, onto drilling:
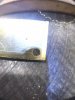
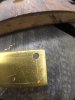
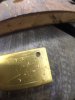
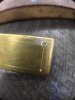
Basically, you just walk up the drill bit sizes. I skip a size with each transition, because life is too damn short.
Also, once you get close to 3/16", you have to step down to 1,200 rpm. The chart says you're good at 3,000 up to 1/4", but when I got one bit before 3/16", the whole thing started to chatter like a college girl on adderall.
I'm gonna stab that calculus exam repeatedly!
Also possibly my boyfriend.
Fortunately, though, the mistake drilled out by the time I got up to 1/4", so my first hole was fine.
So, why didn't I just drill both holes as I went, instead of doing the whole thing twice?
First, I'm a moron. I think we've established that by now.
But second, I wanted to make sure I was going about this the right way, since I'd literally never done this on a drill press before -- I've been using the knee mill up till now, but I wanted to try getting precision on the drill press. That sucker vibrates violently at high speed, and it's not unusual to have to chase middle-aged women away from it at all hours.
Some are pretty adamant about staying.
So once I got into the larger sizes at lower speeds, I went ahead and clamped down my piece. This worked out pretty well.
And now some drill press porn, just because.
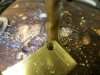
So, lather, rinse, repeat, and I wound up with two perfect 1/4" holes, ready to be marked and cut into four P1 emitter catches on the bandsaw!
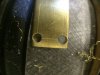
Except, once I got there, the bandsaw wouldn't work. It just went
kachunk when I hit the button. A DC told me the belt was busted, and they were waiting on a new one to come in...
!
And that's when I went off to the computer area to teach myself Inventor by making props with it.
Pictured: Surprisingly, only 12 hours of work!
So hopefully next weekend the bandsaw will be back up and running, and I can either finish making my pieces, or at least practice sewing my fingers back on.