Re: John Long Phaser 1 Kit Buildup plus MM P2 Restoration
Hey, everybody! Lots to post today, so it'll take a while, and there's more than just the fins to talk about. I've been doing other little detail projects too, with varying degrees of success, and I'm actually going to be doing a little work at home even as I clean up around this war zone of an apartment and make sure my suit is nice and pressed and lawy-looking for my new gig tomorrow (I hate it when they demand business attire on the first day of a project. I'm a very "biz casual" kinda guy).
And off we go!
So, fins. Yeah, man... fins...
What a mess I made of this part of the project! Something so simple, and yet I decided I'd get all fancy with it and make The World's Greatest Phaser Fins.
Um, no, it's not, it turns out.
Coincidentally, when I consulted with the head DC
* at Techshop on a related machining issue, he recommended I watch a series of YouTube videos by this guy who goes by "tubalcain." He's a retired shop teacher who's forgotten more about machining metal than most people will ever learn, and his videos are amazing.
This is the link to the one that started me down the road to ruin.
It's a video showing three methods for precisely laying out holes for drilling, two of which use a height gage, and we've got a
sweet height gage in the machine shop.
Just look at all that sweet, height-gagey deliciousness!
The thing to the left of it is... um... one of those big steel machine shop thingies that's, like, all straight and flat and stuff. I don't remember what it's called, but my groin muscles are
really pi§§ed off at it, so maybe it's best we're not on speaking terms.
So I thought to myself, "Self, why not adapt tubalcain's old-timey shop method to make insanely straight and exact cut lines, which I can then make grotesquely jagged when I try to cut them out on the bandsaw?" Okay, not exactly, but that's the way I should've said it to myself. So yeah, it's actually my fault for not warning me I was headed for trouble. My cuts did come out nice and straight later on, just not on the bandsaw....
To set up for this, first you need a very flat, perfectly smooth surface. Machine shops usually have a slab of perfectly ground steel for this, but Techshop doesn't seem to for some reason. Maybe they don't like flat things.
Here's what I came up with at first: a nearby anvil (new to the shop, so I missed it at first glance). But not so great, because there's really no room on it to work. But it was fine for making sure the gage was good and zero was actually zero (and when, you ask, is zero
not zero? When I'm the one doing the math, that's when.
sigh.).
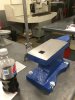
So I realized the welding tables are perfectly flat, and as long as I used the side farthest away from the actual welding positions, it wouldn't be a lunar landscape of tiny steel slag drops. Turned out it was, just much less so, which left me room to set up and slide my gage around with relative ease.
So you start by figuring out the width of your fins, which I got by measuring the ones on my Wand phaser: 0.906", give or take a thousand feet. Meh.
Then you set the height gage to exactly 0.906", after you spend 15 minutes figuring out how to operate a fµçking height gage in the first place. Hint: use your calipers to double-check. It's like math -- if your answer is the same as the one in the back of the book, you did it right (or you got very, very lucky). In fact, it
is math -- no wonder I suck at it.
Once the height gage is set to the correct height, and the bottom edge of the metal you're going to mark is perfectly straight, you just rest the metal against your perfectly vertical slab of groin-killing steel death and drag your height gage across it like this:
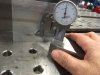
As long as your surface is perfectly flat, your height gage is correct, the nuts are correctly tightened, the bottom edge of your sheet metal is perfectly straight, Dr. Deathslab is perfectly vertical, and there are no tiny little bits of dust or shavings underneath your instruments, it's pretty easy!
So when I saw what a perfectly straight line I could get this way, I thought, "Self, now that you're on a roll, why not mark out the entire fin outline this way, and get perfectly marked-out fins?"
Tell me again how a middle-aged, math-addled lawyer
who can't figure out a tip without his iPhone and a CalTech
consultant is going to calculate those dimensions. I think it's so cute.
I thought I had a picture of this disaster that cost me 30 minutes all by itself, but mercifully I think my iPhone flushed it down the cyberloo. It's really for the best.
So here's where I ran back to mommy, which is what I now call the laser cutter. I just created a template in Illustrator and cut myself out a pair of stencils in acrylic.
The tiny squares in a pile on the left are spacers for the fins. You might notice I used a much smaller sheet of plastic stock than usual and didn't cut out 5 million of these things. There's a rea$on for that.
Once I had the stencils, marking the aluminum was even easier than with the height gage. I just Scotch taped the stencil on the aluminum, and traced it with a machinist's scribe:
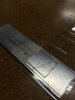
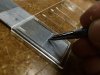
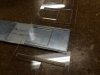
I numbered them 1 - 4 from bottom to top, because it's very easy to confuse them once they're cut out. Funny I didn't think to do that on the actual stencils.
After I cut them out on the bandsaw (which oddly enough went very well), I marked them for filing with a blue Sharpie -- just mark the parts to be filed away, and file them away till there's no more blue.
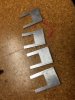
Here's a useful tip: When you're filing the edge of something thin like this, mount it as close as possible to the edge of your vise to maximize control and help keep it from bending out of shape when you file it. You want just the parts you're going to file away to be exposed. I also like to place my front wood block just a hair lower than the rear one, so I'm better able to see my markings. Remember, this only works if you file properly -- in one direction, away from you.
After I finished filing the contours on #1 (the bottom fin), here's how it looked:
And with 2, 3, and 4 staring me in the face, after taking about 30 minutes filing #1 to shape, I suddenly realized. "WTF am I
doing?!"
And that sent me racing back to the machine shop.
More on what I did next in a little bit, but right now I have to do a couple of things around the house to get ready for job tomorrow. (
Job is what I do for a living,
work is what I do at Techshop. The distinction reminds me to keep things in perspective in life, and that way I don't go crazyballs with depression and stick my head in a document shredder while I'm at
job.)
*DC = "Dream Consultant." Yes, it's cheesy. OMG, did I tell you you can totally DIY your own cheese?