zjunlimited
Sr Member
Alrighty, the next build on the bench is the Map to Thrawn from the Ashoka Disney show.
The direction I'm taking with this one is to use the Megaminx ball as the base and the Map tiles from Wonderknight and eethan
(links to their interest/purchase thread and the WIP thread).
I ordered the Megaminx ball from AliExpress and arrived as promised without any issues (whew!). I wanted the all black version but that was all sold out. Only the silver was available so I grabbed it. Wasn't sure yet how to address the silver finish but that will wait for later.
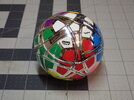
Next was to remove the stickers which came off pretty easy
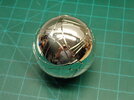
A quick test with some 320 grit sandpaper reveals the black plastic underneath and proceeded to sand the rest of the ball down.
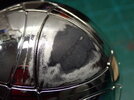
So while that was relatively easy...just took some old fashioned sanding effort, I'm left with the silver in the seams.
I thought about painting the entire ball black to hide the silver but I quickly moved away from that idea.
I really didn't want to disassemble the ball but I don't think I have a choice here...
The direction I'm taking with this one is to use the Megaminx ball as the base and the Map tiles from Wonderknight and eethan
(links to their interest/purchase thread and the WIP thread).
I ordered the Megaminx ball from AliExpress and arrived as promised without any issues (whew!). I wanted the all black version but that was all sold out. Only the silver was available so I grabbed it. Wasn't sure yet how to address the silver finish but that will wait for later.
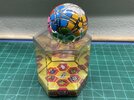
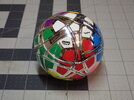
Next was to remove the stickers which came off pretty easy

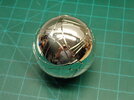
A quick test with some 320 grit sandpaper reveals the black plastic underneath and proceeded to sand the rest of the ball down.
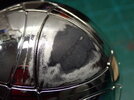
So while that was relatively easy...just took some old fashioned sanding effort, I'm left with the silver in the seams.
I thought about painting the entire ball black to hide the silver but I quickly moved away from that idea.
I really didn't want to disassemble the ball but I don't think I have a choice here...
Last edited: