Lol, thanks
Had to build another helmet for the suit while the other model is getting molded.
Had an unfortunate accident last week on the signed helmet. The helmet fell off my
Bar showing the suit to a contractor. I think my soul left my body when it fell. Fortunately the faceplate survived with a little touch up and looks like new. That will now go into a wall mounted plaque.
Here's the new one, took about 1 week. This one didn't come out to bad. This time I drilled holes and put flat head screws in the sides for the faceplate hinges and works much better. Also coated the inside with a thick coat of zpoxy.
Looks great! Good job.
If i might suggest something.. Make the small edges arround the eye (flat) black and also fill up the lines with some normal acryl black paint. I will give the Helmet much more depth. and maybe some weathering at the top of the faceplate..
Like this:

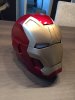