Hexapuma
New Member
Or is it Sabre? I'm never sure.
Anyway, I just started in on this glorious past-time that is replica props and, since I have access to a lathe, I thought I'd start off with an attempt at replicating Luke's RotJ lightsaber based on the plans by Francisco Garcia and Rob Petkau. You can see the first stage below, which is turned from a bar of Alu. Because of the outer diameter of the emitter shield, I elected not to do it all in one piece. Not to mention that the pommel would be tricky to shape.
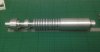
I've 3D printed the pommel cap, which I'm thinking I'll drill through into the pommel tang and tap. Hold in place with a recessed screw. I also need to print the emitter shield, although if I can find a suitable piece of Alu that I can fit in the chuck of my lathe then I might still turn it as a separate piece. Even if I paint the plastic, it's not going to have the same shine as metal.
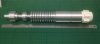
Then it's just a matter of making and mounting the control box and painting the various sections.
I have to admit, looking at all the beautiful sabers people have on here, it's quite intimidating.
Anyway, I just started in on this glorious past-time that is replica props and, since I have access to a lathe, I thought I'd start off with an attempt at replicating Luke's RotJ lightsaber based on the plans by Francisco Garcia and Rob Petkau. You can see the first stage below, which is turned from a bar of Alu. Because of the outer diameter of the emitter shield, I elected not to do it all in one piece. Not to mention that the pommel would be tricky to shape.
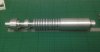
I've 3D printed the pommel cap, which I'm thinking I'll drill through into the pommel tang and tap. Hold in place with a recessed screw. I also need to print the emitter shield, although if I can find a suitable piece of Alu that I can fit in the chuck of my lathe then I might still turn it as a separate piece. Even if I paint the plastic, it's not going to have the same shine as metal.
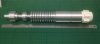
Then it's just a matter of making and mounting the control box and painting the various sections.
I have to admit, looking at all the beautiful sabers people have on here, it's quite intimidating.