Skidmark
New Member
This is only my second stab at pepakura. I own a Roland GX-24 vinyl cutter and decided to force a try at using it to cut the card stock for pepakura. I wanted to start with something intricate so I decided on the Sharkhead / Dubean33- Iron Man Mark VI HD helmet. There is a few steps needed before you can use the file on a vinyl cutter. I first purchased the key for the program thinking that exporting the file to EPS would work, but the export portion does not function properly. So I opted for printing it to file using a PDF printer called foxPDF, but I think as long as a person prints to file and makes sure its in PDF all should be ok no matter the program. Before printing make sure to take off tab nubering on your pep file, this will save you a headache later when cutting. Next I printed a copy of all the pages for a hard copy to refer to as directions. The vinyl cutter still requires another step before it can cut the files. I used CorelX to open the file and export it to EPS. After exporting to EPS I opened that file in Roland Cut Studio were it is prepared for the vinyl cutter by simply adjusting the image for the cutter's loaded paper. To cut the paper you need a backing on the cardstock. I used one from Criket that I purchased at Hobby Lobby for 20 dollars(pack of 2). Speed of the cutter was set to 15 cm/2nd and 150lbs pressure. To load and cut all 10 sheets took only an hour. To adjust the file in Pepakura designer, print to file, open in Corel Drax, export and load to Roland Cut studio took about thirty minutes. Total time to adjust and cut was about an hour and a half. A big bonus was the cutter also cuts the fold lines which helps out later in time saving versus cutting with a razor knife and trying to eyeball and estimate folds. *note some very narrow folds in the circumference of the HD helmet still gave me headaches.
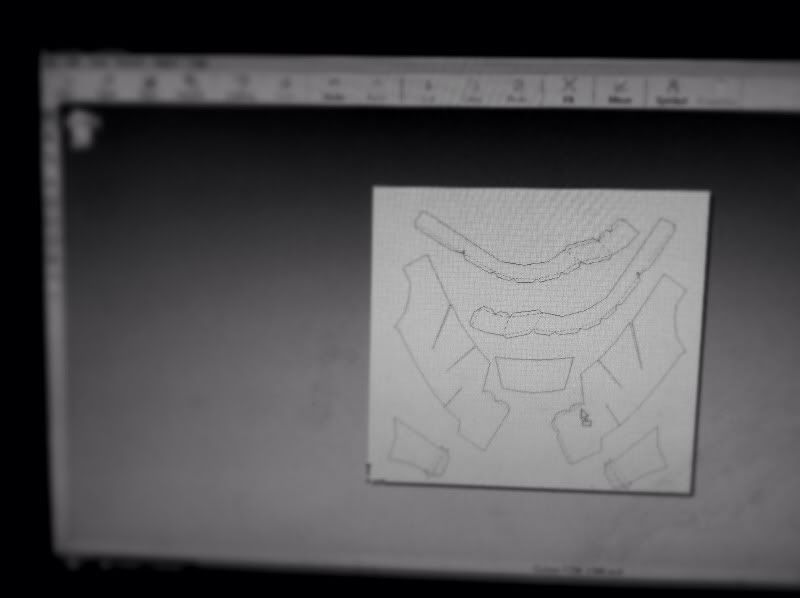

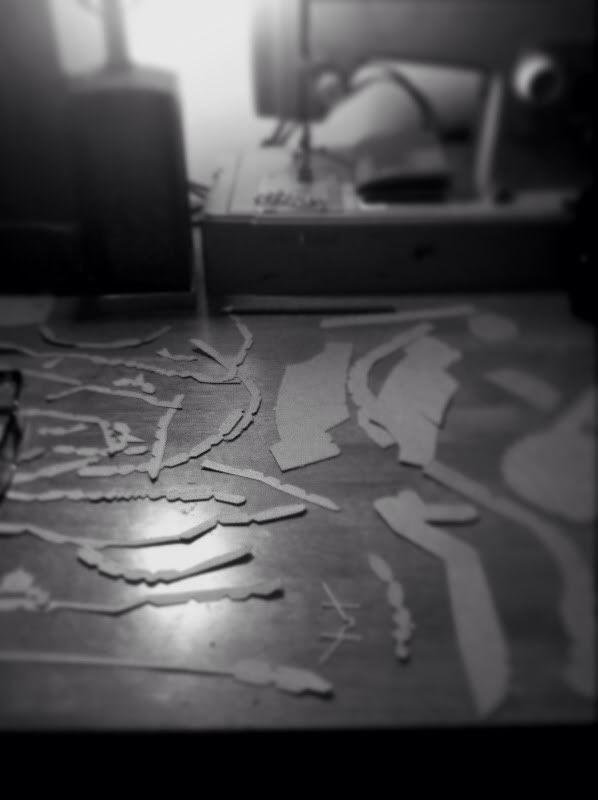
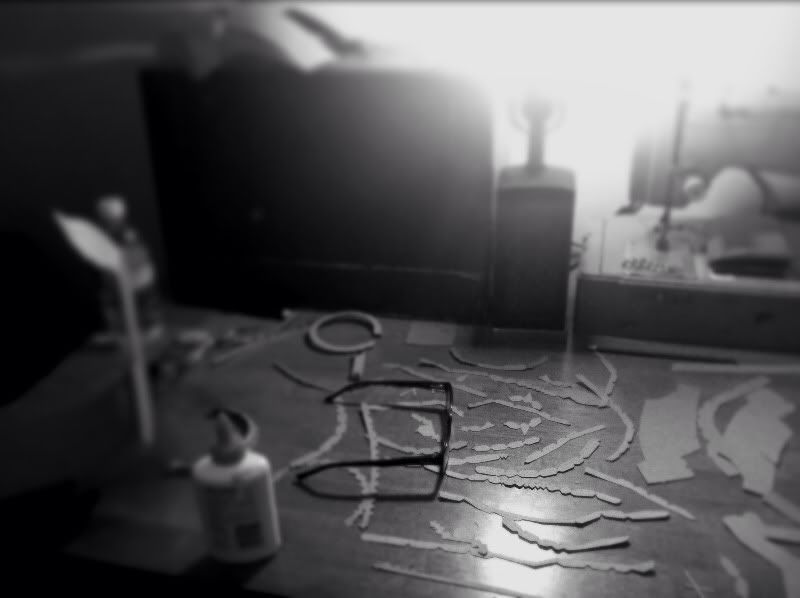
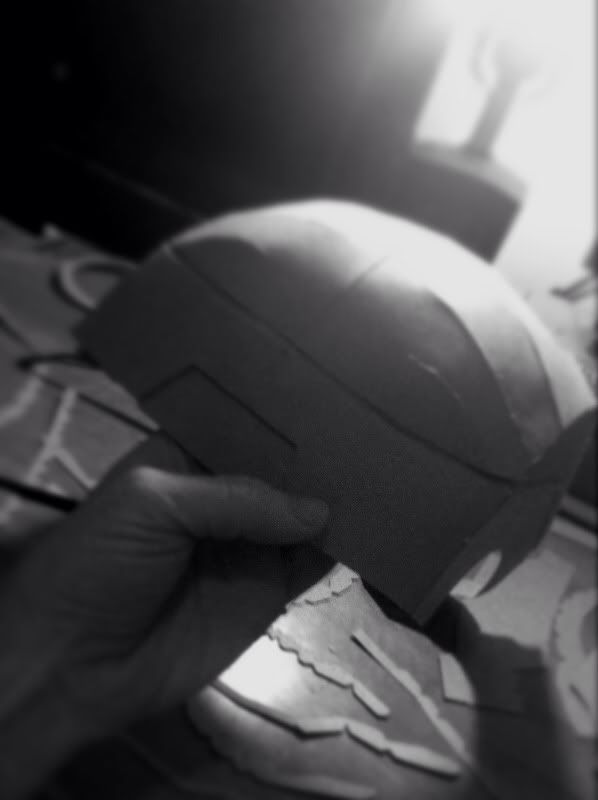
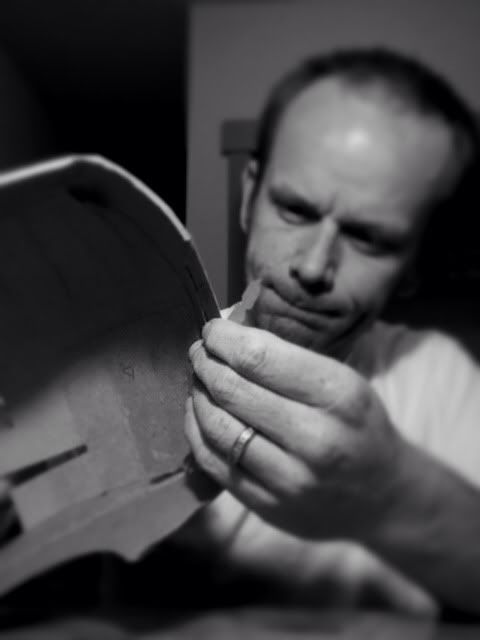
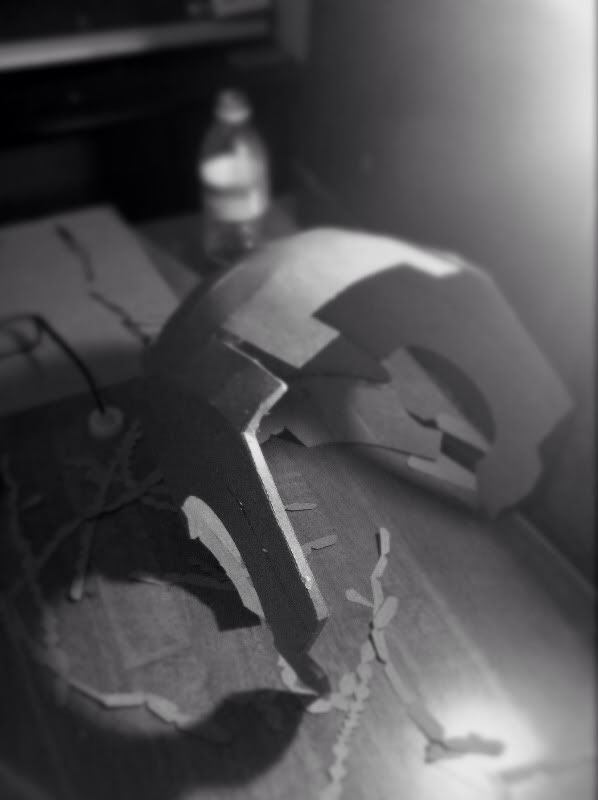
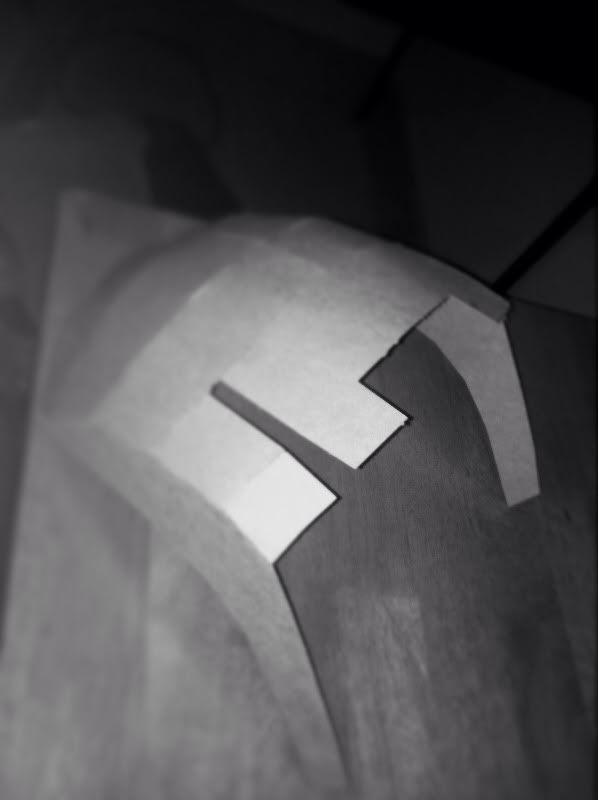
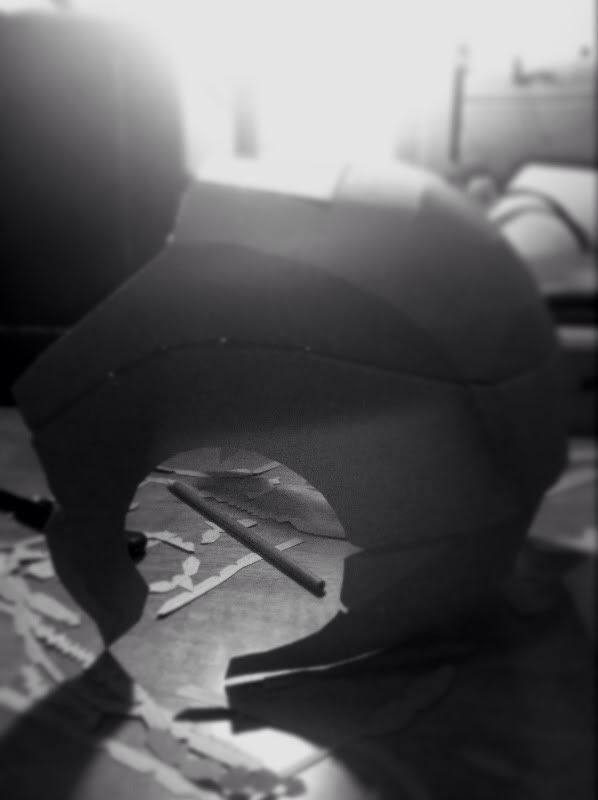
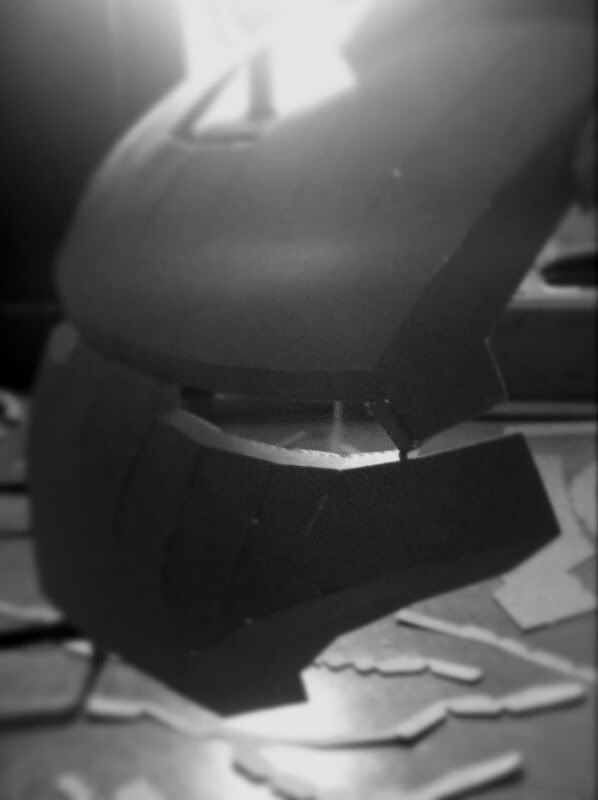
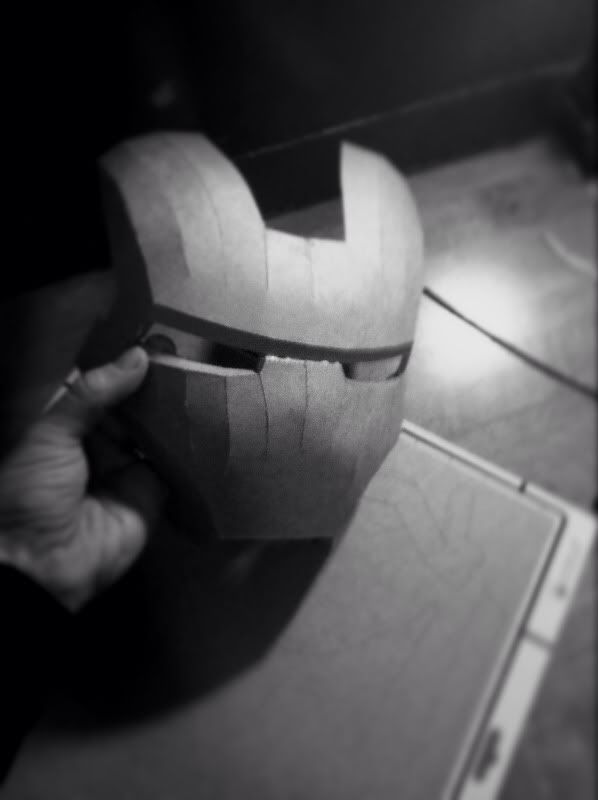
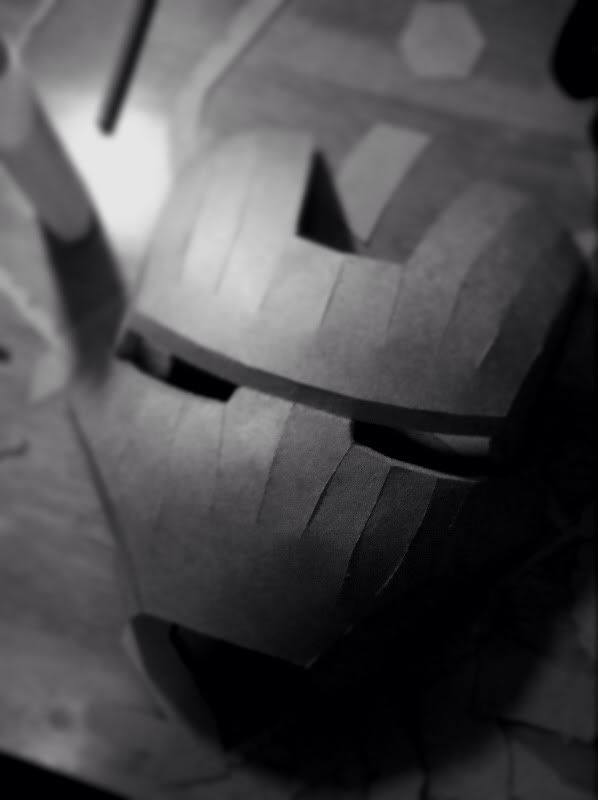
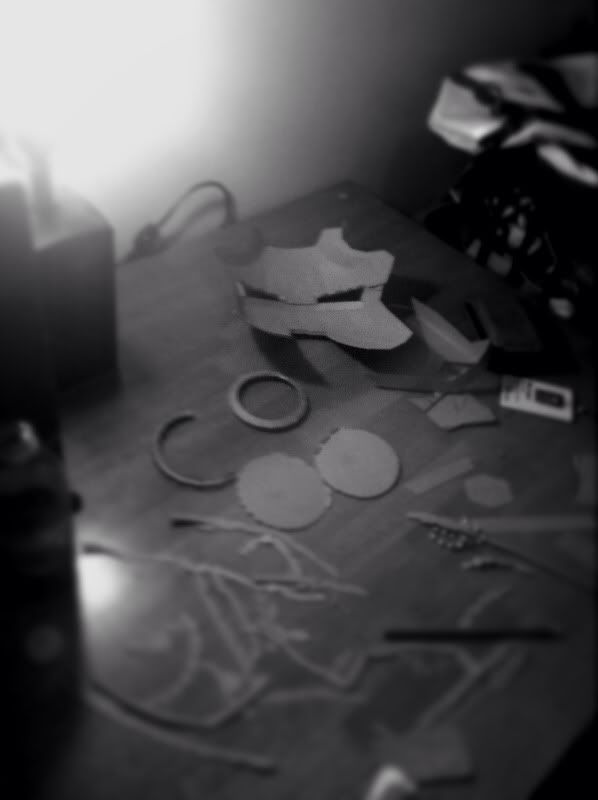
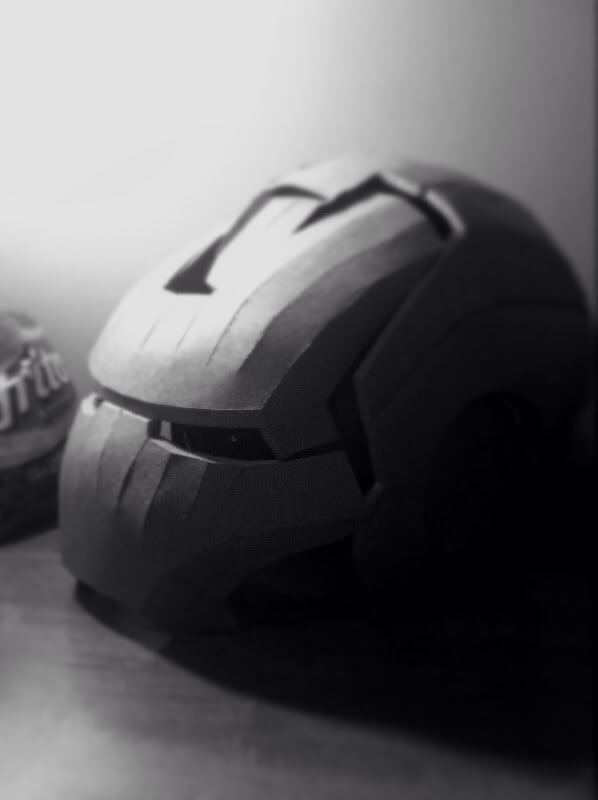
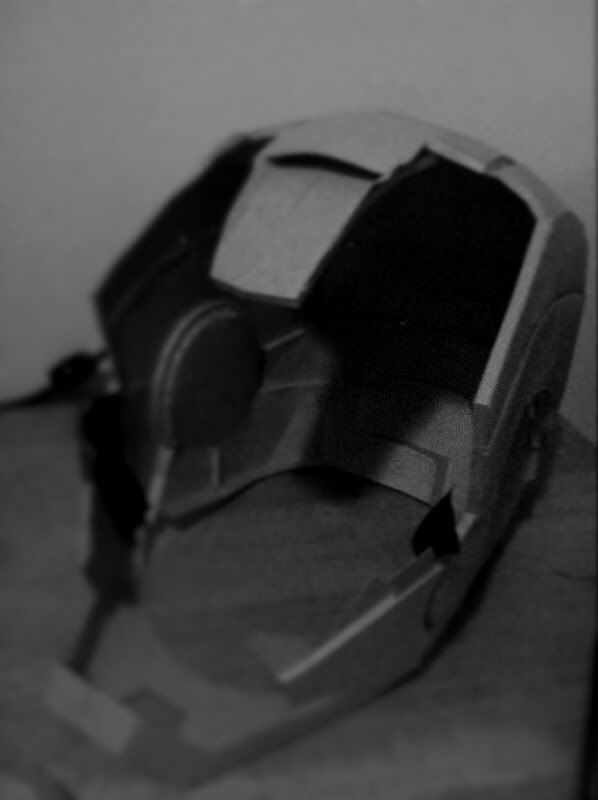
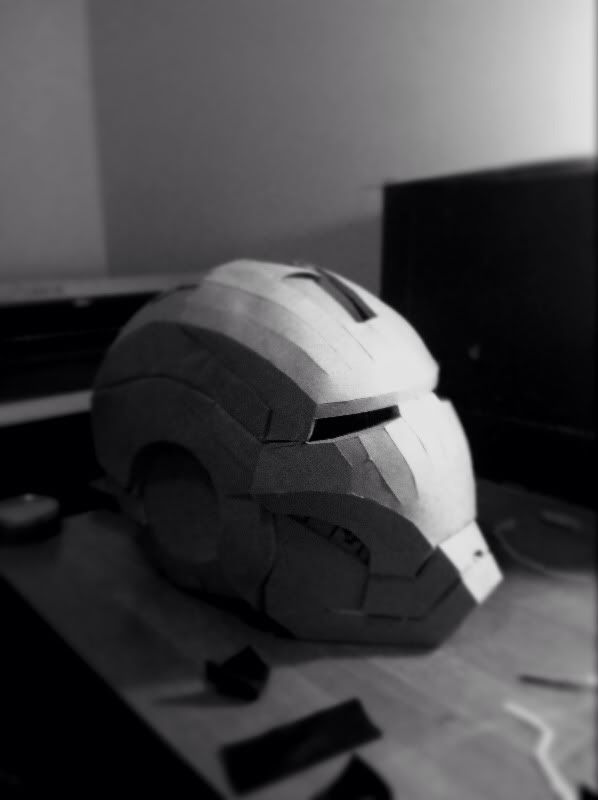
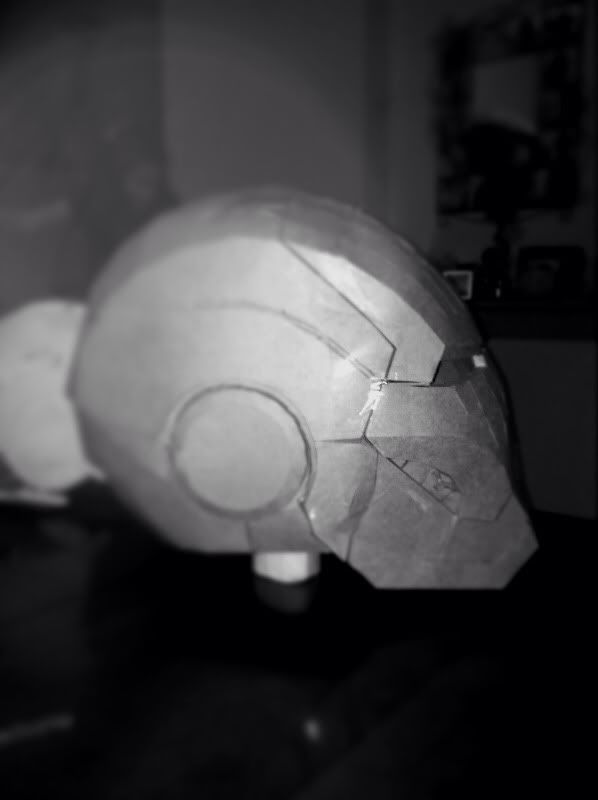
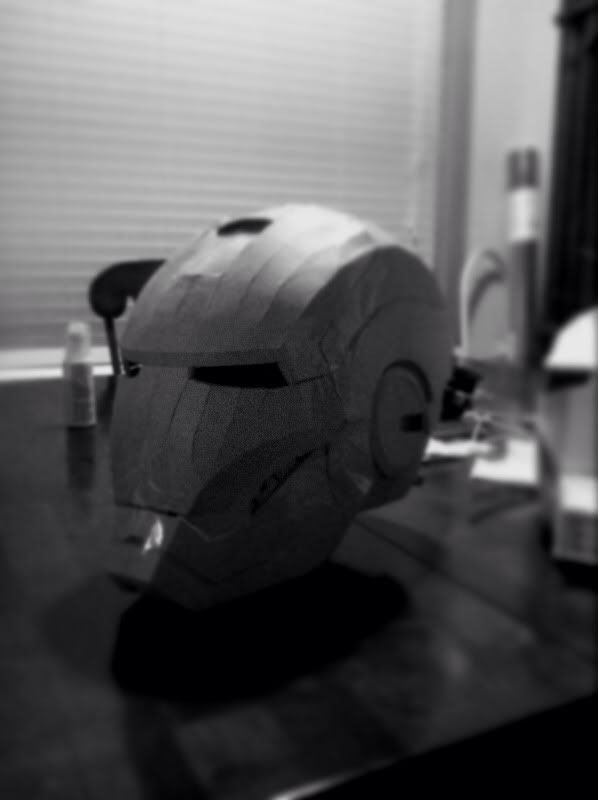
Last edited: