Gallagher
New Member
About a year ago, we decided we wanted to make the iconic iron helmet out of Bethesda's landmark shouting simulator, the Elder Scrolls V: Skyrim.
This was the target:
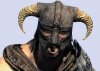
As this was my first build, a heavy emphasis was placed on the pre-planning. Heavy inspiration was drawn from the process of Harrison Krix, better known as Volpin. Our build process is essentially a cut and paste of his, but with more errors. We began by scaling a front, side, and top angle to life size.
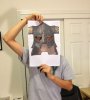
Looking good already!
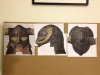
From there, we mounted the images onto mdf board and cut them out with a hand fret saw.
The pieces were then slotted and assembled, giving us a basic framework to sculpt over.
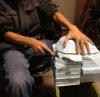
From there, solid insulation foam was cut to size and glued in, and the early shape of the helmet took form:
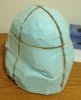
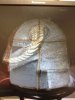
Using cutting edge photoshop technology, an overlay of the in-game model and our foam block was made, which made shaping much less of an ordeal.
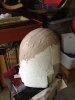
After we reached an initial shape we were happy with, the foam was painted over to protect it from the corrosive effects of the bondo we added afterwards.
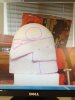
The bondo was used to smooth out the helmet and get a better look at where the final details (the horns, eyes, rivets, etc.) would end up on the finished product.
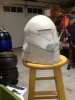
After the bondo had its run, we moved on to epoxy sculpt for the finer details. It starts out smooth and workable, but hardens to rock in 24 hours.
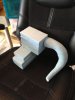
While this was going on, we started the shaping of the horns. Pulling two identically smooth cylinders out of bricks of foam was an adventure in and of itself.
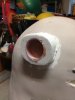
Foam inserts were attached to the bondo'd form with more bondo and served as the mounting points for the horns. Plastic tea candle holders were Macgyver'd into ram horn mounts.
The horns were mounted into the helmet for the first time, and if I squinted really hard it was starting to look pretty good.
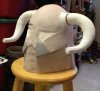
The front region of the face took form next. The little dots of epoxy sculpt that formed the rivets entertained me for days.
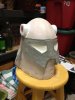
Not only that, but the horns were starting to look like real horns! Seeing the whole look come together for the first time was easily the high point of the whole build.
The sculpting process was practically over at this point. The molding process would begin soon.
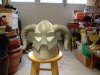
The horns and helmet were spray-painted glossy red to better accentuate any blemishes still remaining, as well as to cut down on any parts sticking to the mold.
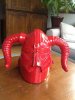
The mold supplies started to show up at our doorstep around this point, so we decided to pull the trigger and begin the molding process.
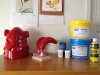
We started with a very thin layer of silicone on the horns to capture all the little bumps and grooves.
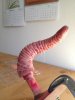
From there, we painted on a second and third layer, each significantly thicker than the last.
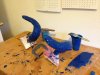
With the molding of the helmet coming up the horizon we decided to give the aluminum powder a quick test run with a quarter. On the final product, this powder provided the metallic sheen.
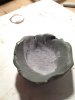
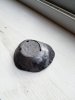
Spectacular.
The molding of the helmet began next.
This was the target:
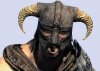
As this was my first build, a heavy emphasis was placed on the pre-planning. Heavy inspiration was drawn from the process of Harrison Krix, better known as Volpin. Our build process is essentially a cut and paste of his, but with more errors. We began by scaling a front, side, and top angle to life size.
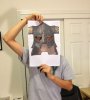
Looking good already!
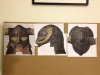
From there, we mounted the images onto mdf board and cut them out with a hand fret saw.
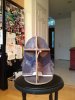
The pieces were then slotted and assembled, giving us a basic framework to sculpt over.
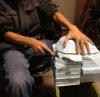
From there, solid insulation foam was cut to size and glued in, and the early shape of the helmet took form:
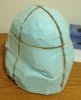
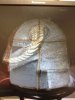
Using cutting edge photoshop technology, an overlay of the in-game model and our foam block was made, which made shaping much less of an ordeal.
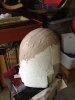
After we reached an initial shape we were happy with, the foam was painted over to protect it from the corrosive effects of the bondo we added afterwards.
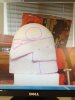
The bondo was used to smooth out the helmet and get a better look at where the final details (the horns, eyes, rivets, etc.) would end up on the finished product.
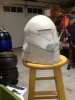
After the bondo had its run, we moved on to epoxy sculpt for the finer details. It starts out smooth and workable, but hardens to rock in 24 hours.
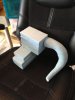
While this was going on, we started the shaping of the horns. Pulling two identically smooth cylinders out of bricks of foam was an adventure in and of itself.
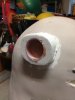
Foam inserts were attached to the bondo'd form with more bondo and served as the mounting points for the horns. Plastic tea candle holders were Macgyver'd into ram horn mounts.
The horns were mounted into the helmet for the first time, and if I squinted really hard it was starting to look pretty good.
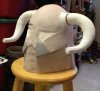
The front region of the face took form next. The little dots of epoxy sculpt that formed the rivets entertained me for days.
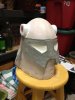
Not only that, but the horns were starting to look like real horns! Seeing the whole look come together for the first time was easily the high point of the whole build.
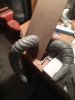
The sculpting process was practically over at this point. The molding process would begin soon.
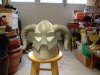
The horns and helmet were spray-painted glossy red to better accentuate any blemishes still remaining, as well as to cut down on any parts sticking to the mold.
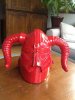
The mold supplies started to show up at our doorstep around this point, so we decided to pull the trigger and begin the molding process.
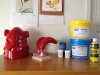
We started with a very thin layer of silicone on the horns to capture all the little bumps and grooves.
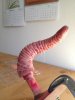
From there, we painted on a second and third layer, each significantly thicker than the last.
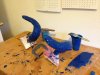
With the molding of the helmet coming up the horizon we decided to give the aluminum powder a quick test run with a quarter. On the final product, this powder provided the metallic sheen.
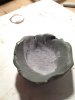
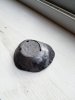
Spectacular.
The molding of the helmet began next.