Riceball
Master Member
I'm relatively new to the whole costuming and prop thing and don't have any experience with the methods used by the pros here but I know what I want to do and have a rough idea of how to do it but I need help with the details though. What I'm trying to do is to use a cheapy set of vac formed Halloween store grade Roman muscle cuirass as a mold for making one more to my tastes based on the type seen in Rome and Spartacus. To do that I plan on filling all of the details and other unwanted parts with clay and then laying glass in it to create a plain curiass/breast plate that I'll attach my own decorations to. But having no experience with fiberglass or anything similar I don't know if I can apply the resin directly to the plastic with some basic mold release or would I need something more specialized or would I need to fill the interior with another material or clay?
I would also appreciate any suggestions for casting materials, any alternatives/better solutions to regular fiberglass resin or a particular type or brand of resin? Any general tips and/or suggestions for working with the stuff would also be greatly appreciated; things like how to apply the resin to get a smooth surface, things not to do, things to get best results, etc. All help would be most greatly appreciated.
Here's what I'm working with:
And here's an example of what I'm trying to make it look more like:
I would also appreciate any suggestions for casting materials, any alternatives/better solutions to regular fiberglass resin or a particular type or brand of resin? Any general tips and/or suggestions for working with the stuff would also be greatly appreciated; things like how to apply the resin to get a smooth surface, things not to do, things to get best results, etc. All help would be most greatly appreciated.
Here's what I'm working with:
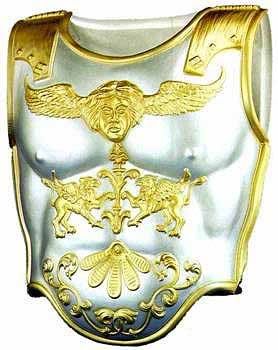
And here's an example of what I'm trying to make it look more like:
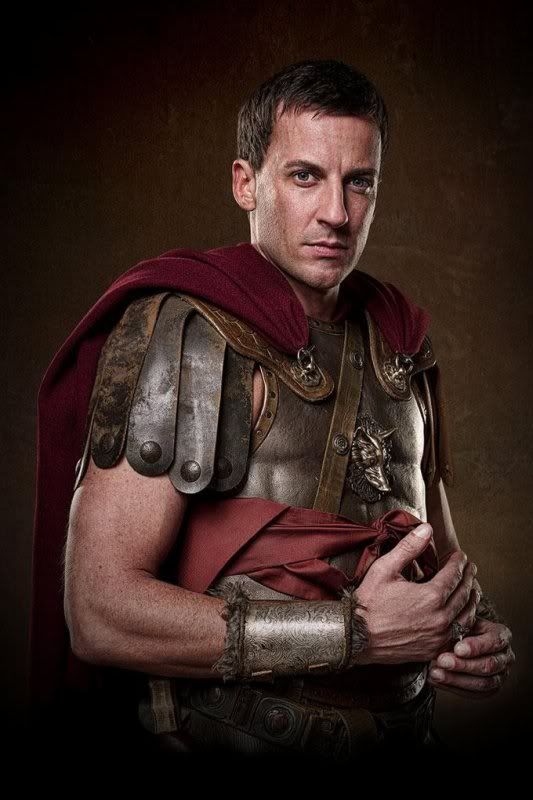
Last edited: