LizardJedi
Sr Member
OK I have to say first off, that I've been searching around a reading a lot of old threads about this, and I'm learning a lot. But this will be my first time playing with this kind of stuff, and its a big group project, so I can't screw up!
Long story short, we need to make some airplane wings. Each wing is made up of 2 parts (so 4 parts total) and size wise, the biggest part is about 3'x1'x1.5"
I know there are way that RC people do their wings, but we're starting totally from scratch here.
I came up with a couple ideas, and I would like some input on how I can refine them to be most accurate, and maybe some guidance to if they are even possible (or feasible enough to do)
Since I needed to sketch these up anyway, and because its a lot easier for me to explain things, I snapped a picture of my sketches (scanner isn't hooked up ATM)
Sorry for the bad penmanship...
So, it break it down..
1) CNC the wing out of pink foam. Seal it (latex paint?), then lay some fiberglass over the top. Somehow the FG has to be smooth and even on top... so I guess vacuum bag the FG?
Then, we can either use it as is, or I suppose we can make it hollow, and get rid of the pink foam with some laquer thinner to dissolve it out.
2) CNC a negative mold for both sides out of wood or MDF. Seal this (with paint?) and tons of mold release. Use this as a fiberglass mold. CNC some supports out of metal or carbon fiber (or whatever else we have laying around).
What I don't know about this method is if we would have to glass each mold seperatly and then join them after they cure, or if we could sandwhich them together with the supports, as shown in my sketch. I have a feeling we would have to do the former?
3) Just a mix of 1 and 2... make both a negative and positive mold, glass the negative mold, put the positive molde inside, and sandwhich together (the supports could be included, if the positive was made out of sealed pink foam in sections, with the supports attatched.)
I also had an idea with the negative mold to vacuuform styrene in it (which would probably give the smoothest finish) then glass the styrene. But the vactable we have access to isnt that big. Cutting in sections is an option (in my mind) but the other people in the group don't think its strong enough.
The most important thing in this whole operation is how smooth the surface is. Spending all of our time filling and sanding isn't really an option either.
Time is also of the essense. Honestly, I'd like to try all 3 ways, but this has to be done yesterday. :unsure
So, you glassing and casting Gods of the RPF, help me figure out what to do!
Long story short, we need to make some airplane wings. Each wing is made up of 2 parts (so 4 parts total) and size wise, the biggest part is about 3'x1'x1.5"
I know there are way that RC people do their wings, but we're starting totally from scratch here.
I came up with a couple ideas, and I would like some input on how I can refine them to be most accurate, and maybe some guidance to if they are even possible (or feasible enough to do)
Since I needed to sketch these up anyway, and because its a lot easier for me to explain things, I snapped a picture of my sketches (scanner isn't hooked up ATM)
Sorry for the bad penmanship...
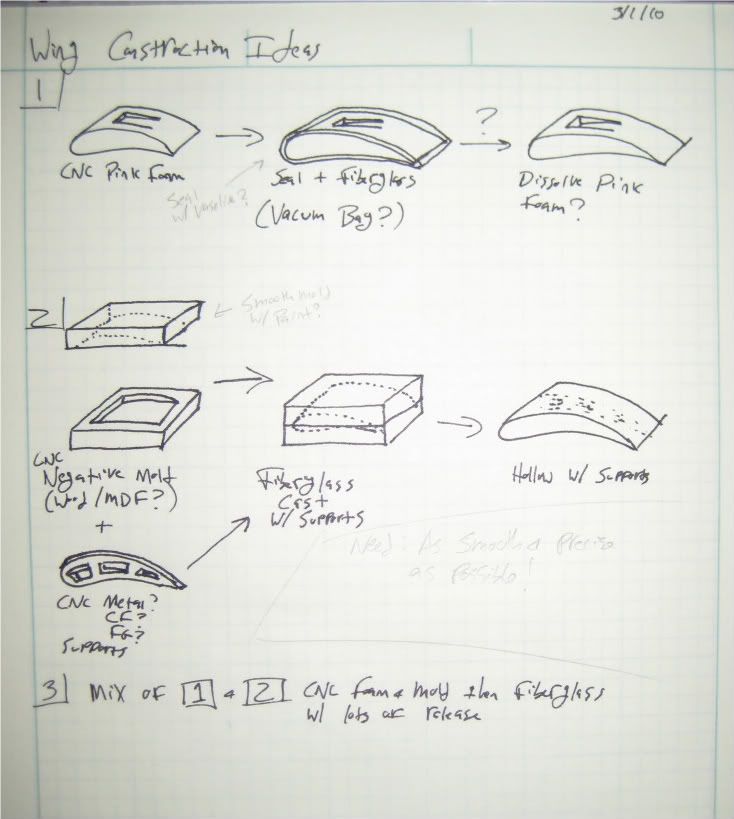
So, it break it down..
1) CNC the wing out of pink foam. Seal it (latex paint?), then lay some fiberglass over the top. Somehow the FG has to be smooth and even on top... so I guess vacuum bag the FG?
Then, we can either use it as is, or I suppose we can make it hollow, and get rid of the pink foam with some laquer thinner to dissolve it out.
2) CNC a negative mold for both sides out of wood or MDF. Seal this (with paint?) and tons of mold release. Use this as a fiberglass mold. CNC some supports out of metal or carbon fiber (or whatever else we have laying around).
What I don't know about this method is if we would have to glass each mold seperatly and then join them after they cure, or if we could sandwhich them together with the supports, as shown in my sketch. I have a feeling we would have to do the former?
3) Just a mix of 1 and 2... make both a negative and positive mold, glass the negative mold, put the positive molde inside, and sandwhich together (the supports could be included, if the positive was made out of sealed pink foam in sections, with the supports attatched.)
I also had an idea with the negative mold to vacuuform styrene in it (which would probably give the smoothest finish) then glass the styrene. But the vactable we have access to isnt that big. Cutting in sections is an option (in my mind) but the other people in the group don't think its strong enough.
The most important thing in this whole operation is how smooth the surface is. Spending all of our time filling and sanding isn't really an option either.
Time is also of the essense. Honestly, I'd like to try all 3 ways, but this has to be done yesterday. :unsure
So, you glassing and casting Gods of the RPF, help me figure out what to do!