CaptainMorgan
Member
This is originally a thread I put over on cosplay.com a while back and got no reception. I mostly used it as a build log, but I think you guys will appreciate.
First off, I did all of these for the sole purpose of doing an out of armor Tony Stark. When I actually do a Ironman suit of armor I'll build a separate version to fit into the chest piece.
With that said I wanted to make an oversized arc reactor on purpose to make it easier to see/notice in costume. I also wanted to make it as thin as possible to seem as if embedded in my chest.
So two years ago I whipped together a quick Tony Stark costume for my first con ever, DragonCon 2010. Here is what I was working with.
This was my quick and dirty arc reactor for the costume that I whipped together in the two days before the con with using minimal fabrication. I ordered the LEDs and then the rest was made out of stuff around the house and the housing of a large tap light.
Turned out decent for an under the shirt arc reactor, but this time I mean business.
First off I'm going to go ahead and give Tuxedo Tony a run since I bought my very own designer Tux for my wedding last May. Here is me in my Tux on my honeymoon cruise alongside Tony Stark in the Tux. I'm not all done up like Tony, but you can compare the Tuxedos and see they are pretty much identical. I have also ordered a Tuxedo shirt without pleats to match Tony's and let the light show through better.
A couple of my costume props just for your enjoyment. Bow tie and me Tony Stark sun glasses. I have a short highball glass in the mail to complete the accessories.
First off, I did all of these for the sole purpose of doing an out of armor Tony Stark. When I actually do a Ironman suit of armor I'll build a separate version to fit into the chest piece.
With that said I wanted to make an oversized arc reactor on purpose to make it easier to see/notice in costume. I also wanted to make it as thin as possible to seem as if embedded in my chest.
So two years ago I whipped together a quick Tony Stark costume for my first con ever, DragonCon 2010. Here is what I was working with.

This was my quick and dirty arc reactor for the costume that I whipped together in the two days before the con with using minimal fabrication. I ordered the LEDs and then the rest was made out of stuff around the house and the housing of a large tap light.
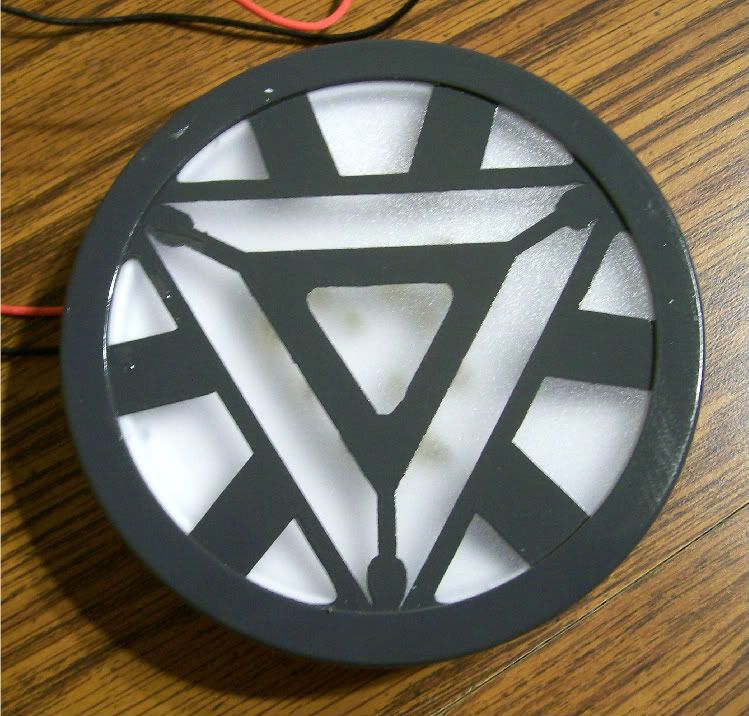
Turned out decent for an under the shirt arc reactor, but this time I mean business.
First off I'm going to go ahead and give Tuxedo Tony a run since I bought my very own designer Tux for my wedding last May. Here is me in my Tux on my honeymoon cruise alongside Tony Stark in the Tux. I'm not all done up like Tony, but you can compare the Tuxedos and see they are pretty much identical. I have also ordered a Tuxedo shirt without pleats to match Tony's and let the light show through better.
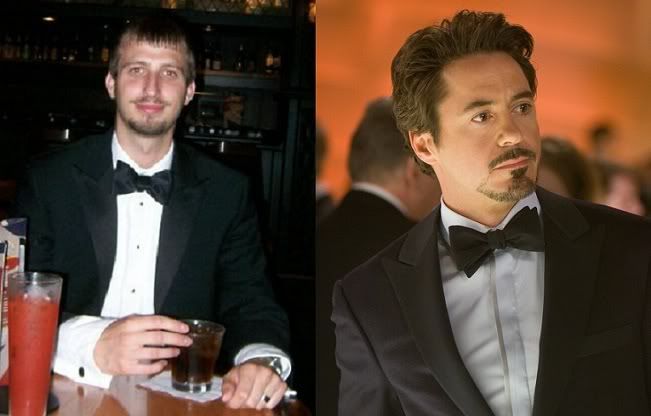
A couple of my costume props just for your enjoyment. Bow tie and me Tony Stark sun glasses. I have a short highball glass in the mail to complete the accessories.
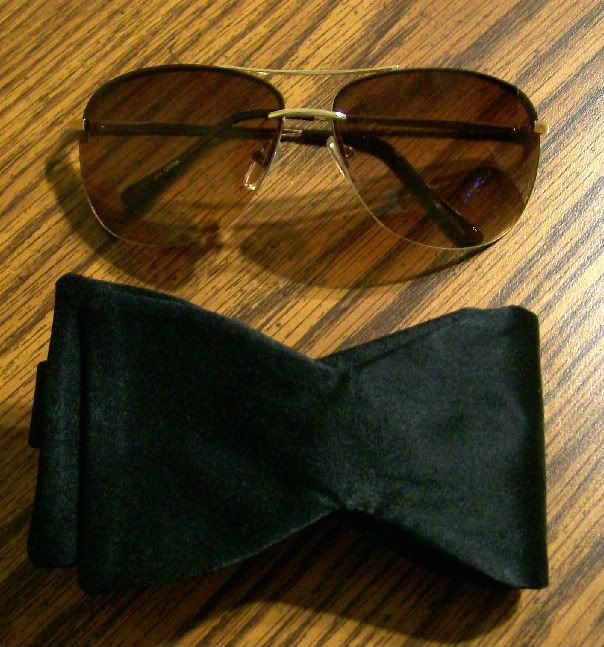