ZMan941
New Member
So a few weeks back I decided to try and revamp my Naked Snake / Big Boss costume to be actually accurate. people got the costume (especially with the box) but it wasn't good enough for me at all. The convention I have been pulling this together for is in 10 days so there will still be some issues with the overall costume, but it will be night and day compared to the previous hodge-podge attempt.
Most of the stuff is pretty easy when you compare to other props/costumes as it is just a matter of finding the right items and piecing them together properly (relatively speaking). The STABO harness is what got me to this board (thanks to TheRonin!) and that just leaves the most other difficult part: the CQC knife. Finding a close-looking knife isn't that hard and others have found them, one being the Fury Glacier Bay. However the problem with real knives is that you can't go around posing with them or even taking them out of the sheaths at any convention I have been to. Naturally there are no rubber prop knives as close as real ones so that got me thinking.
We recently got a 3D printer at work and a coworker mentioned trying to print parts for a cosplay of his and it clicked that the CQC knife made out of PLA or ABS would be a perfect idea. At the same time, this also would allow me to make the knife as close as possible to the game. The office was pretty dead today so I got working on the knife.
Using screenshots, renders, the action figures, and some other prop drawings, I managed to get a scale going and rough out the shape. From there it was a lot of measuring tiny photos and squinting. Lots of squinting.
I took a lot of WIP shots and went through 4 iterations of the shape and details before I got to where I am now. I decided not to post all of them as I feel most people won't exactly care. Where I am right now is based off primarily game screens and the 1/6th scale action figure. Someone has several albums of pictures of just the action figures, including Big Boss / Naked Snake, Solid Snake, and Old Snake. Here is also a close-up of the knife for the 1/6th scale figure.
What I have currently modeled is below:
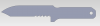
The knife is currently a flat piece. The idea was that however it was created for a prop, it would be finished as needed blade-wise. For some cases doing nothing might be the safest bet. While it won't look the best, it will be clear to people that it has no blade.
Some issues I have run into reference wise are blade shape:
-Some references show a drop point while others show a clip point. I am currently leaning towards a slight clip point.
-The shape of the serrations. This one has them based off the toy. The real-life "kinda close" knives all have square notches rather than proper serrations and it looks strange. I honestly thing it is because they are low-end knives that are stamped rather than having the serrations cut out a bit more finely.
I also kept some things off as this is intended to be made on a thremoplastic extrusion type AMM/3D Printer. Some edges were not rounded off or given certain textures to keep things easier. I intend to take some sandpaper, a file, or a rotary tool to it after it is done.
Also due to the side of the machine I have to make this on, I will be splitting the knife into two parts at the flat protrusion of a hilt. The build area is only 6" x 6" and that seemed like the easiest place for reassembly. After that it will be a matter of wrapping the handle area with paracord.
I hope to do a test print tomorrow.
Please let me know if you have any tips or pointers!
Thanks,
-ZMan
---Edited 4/7/2015---
I changed the name of the thread as I have started a model of the elusive VOX/PTT switch box.
Most of the stuff is pretty easy when you compare to other props/costumes as it is just a matter of finding the right items and piecing them together properly (relatively speaking). The STABO harness is what got me to this board (thanks to TheRonin!) and that just leaves the most other difficult part: the CQC knife. Finding a close-looking knife isn't that hard and others have found them, one being the Fury Glacier Bay. However the problem with real knives is that you can't go around posing with them or even taking them out of the sheaths at any convention I have been to. Naturally there are no rubber prop knives as close as real ones so that got me thinking.
We recently got a 3D printer at work and a coworker mentioned trying to print parts for a cosplay of his and it clicked that the CQC knife made out of PLA or ABS would be a perfect idea. At the same time, this also would allow me to make the knife as close as possible to the game. The office was pretty dead today so I got working on the knife.
Using screenshots, renders, the action figures, and some other prop drawings, I managed to get a scale going and rough out the shape. From there it was a lot of measuring tiny photos and squinting. Lots of squinting.
I took a lot of WIP shots and went through 4 iterations of the shape and details before I got to where I am now. I decided not to post all of them as I feel most people won't exactly care. Where I am right now is based off primarily game screens and the 1/6th scale action figure. Someone has several albums of pictures of just the action figures, including Big Boss / Naked Snake, Solid Snake, and Old Snake. Here is also a close-up of the knife for the 1/6th scale figure.
What I have currently modeled is below:
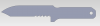
The knife is currently a flat piece. The idea was that however it was created for a prop, it would be finished as needed blade-wise. For some cases doing nothing might be the safest bet. While it won't look the best, it will be clear to people that it has no blade.
Some issues I have run into reference wise are blade shape:
-Some references show a drop point while others show a clip point. I am currently leaning towards a slight clip point.
-The shape of the serrations. This one has them based off the toy. The real-life "kinda close" knives all have square notches rather than proper serrations and it looks strange. I honestly thing it is because they are low-end knives that are stamped rather than having the serrations cut out a bit more finely.
I also kept some things off as this is intended to be made on a thremoplastic extrusion type AMM/3D Printer. Some edges were not rounded off or given certain textures to keep things easier. I intend to take some sandpaper, a file, or a rotary tool to it after it is done.
Also due to the side of the machine I have to make this on, I will be splitting the knife into two parts at the flat protrusion of a hilt. The build area is only 6" x 6" and that seemed like the easiest place for reassembly. After that it will be a matter of wrapping the handle area with paracord.
I hope to do a test print tomorrow.
Please let me know if you have any tips or pointers!
Thanks,
-ZMan
---Edited 4/7/2015---
I changed the name of the thread as I have started a model of the elusive VOX/PTT switch box.
Last edited: