dbsamurai
Active Member
Hiya everyone. Noticed someone was kind enough to upload the power armor frame as a pep file, which means I can begin work on my insane plan.
Here's a rough image of the initial gameplan
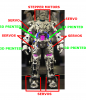
So the gameplan is to build power armor...functioning (to an extent) power armor, in that it will be one size fits most and open and close to allow you to climb into it as an automated function.
In order to execute this, I'm planning on servo powering the hinges tied to a microcontroller in the chest with a button in the forearm and a button the back fusion core that'll open and close the armor. The ankle servos there (may be one...may be 2, I'll see how much torque I need) will be for opening the calves, not powering the armor ankles. I'm also planning on a stepper motor or some other dedicated motors for the shoulder openers because of the amount of weight they'll be carrying.
The pink parts I'm planning on being real Rubber, likely 3d printed simply because it's easier than making the necessary rubber molds to make bendable tubing. The blue markings will probably be purchased tubing from home depot or fry's or whatever, something flexible as cabling that I'll probably even use to store the wires for the servos and stuff.
In order to make it one size fits most (and this will be implemented last of all), the foot pads will feature telescoping foot pads to raise or lower people based on their height, the hand controlls will similarly telescope further into the forearms to allow shorter arms to reach them. Finally, as an absolute last resort to make sure it can fit people 6'5" to 5'2" tall, will make the chest adjustable, allowing it to be slid down over the abs further to accomodate shorter chests. Also this adjustment is planned to require tightening and loosening of bolts, so it won't be a "quick" transition, more of a fast fitting.
The goal for the overall function is to make it as in game accurate as I can (within reason, considering how the armor clips) so that will necessitate moving ankles with my feet above the actual feet. The gameplan for this is to make an ankle hinge, and attach springs or hydraulic extenders (like you'd find on your trunk) to the toes and ankles of the feet and the toes and ankles of the footclips, to allow you to bend the ankles but with a large enough resistance to prevent the weight of the armor itself from toppling the ankle (so that'll necessitate using springs/hydraulics with sufficient forces to withstand the torsional force of the armor itself...they'll no doubt need to be increased as I produce more of the armor and the weights turn out to be larger than I calculated)
The armor feet will probably be rubber soles and aluminum braces sandwiched around an aluminum sheet/plate to give them sufficient strength while still being light, and providing ample strenght to mount the springs to without bending.
As for the frame, the gameplan is to pull a Thorssolli (whom I'm drawing a lot of inspiration from for this build) and vacuum form everything for the most part, save for the hands themselves which will be 3d printed or laser cut mechanisms to allow me to grab things (because I learned from Gipsy how much it sucks not having hands...) so that'll be exciting...I'll likely have to fabricate my own vacuum former to accomodate some of the pieces too, consdiering their size.
It should take me a while to get the frame done, so hopefully that'll give everyone who's ripping files from the game more time, cause I'm hoping to get the over armor to be the X-01 (since it has the least amount of clipping and has a helmet that can most easily be modified to not clip into the back when it opens).
The overarmor will also be vacuum formed and then bolted onto the frame.
Here's a rough image of the initial gameplan
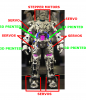
So the gameplan is to build power armor...functioning (to an extent) power armor, in that it will be one size fits most and open and close to allow you to climb into it as an automated function.
In order to execute this, I'm planning on servo powering the hinges tied to a microcontroller in the chest with a button in the forearm and a button the back fusion core that'll open and close the armor. The ankle servos there (may be one...may be 2, I'll see how much torque I need) will be for opening the calves, not powering the armor ankles. I'm also planning on a stepper motor or some other dedicated motors for the shoulder openers because of the amount of weight they'll be carrying.
The pink parts I'm planning on being real Rubber, likely 3d printed simply because it's easier than making the necessary rubber molds to make bendable tubing. The blue markings will probably be purchased tubing from home depot or fry's or whatever, something flexible as cabling that I'll probably even use to store the wires for the servos and stuff.
In order to make it one size fits most (and this will be implemented last of all), the foot pads will feature telescoping foot pads to raise or lower people based on their height, the hand controlls will similarly telescope further into the forearms to allow shorter arms to reach them. Finally, as an absolute last resort to make sure it can fit people 6'5" to 5'2" tall, will make the chest adjustable, allowing it to be slid down over the abs further to accomodate shorter chests. Also this adjustment is planned to require tightening and loosening of bolts, so it won't be a "quick" transition, more of a fast fitting.
The goal for the overall function is to make it as in game accurate as I can (within reason, considering how the armor clips) so that will necessitate moving ankles with my feet above the actual feet. The gameplan for this is to make an ankle hinge, and attach springs or hydraulic extenders (like you'd find on your trunk) to the toes and ankles of the feet and the toes and ankles of the footclips, to allow you to bend the ankles but with a large enough resistance to prevent the weight of the armor itself from toppling the ankle (so that'll necessitate using springs/hydraulics with sufficient forces to withstand the torsional force of the armor itself...they'll no doubt need to be increased as I produce more of the armor and the weights turn out to be larger than I calculated)
The armor feet will probably be rubber soles and aluminum braces sandwiched around an aluminum sheet/plate to give them sufficient strength while still being light, and providing ample strenght to mount the springs to without bending.
As for the frame, the gameplan is to pull a Thorssolli (whom I'm drawing a lot of inspiration from for this build) and vacuum form everything for the most part, save for the hands themselves which will be 3d printed or laser cut mechanisms to allow me to grab things (because I learned from Gipsy how much it sucks not having hands...) so that'll be exciting...I'll likely have to fabricate my own vacuum former to accomodate some of the pieces too, consdiering their size.
It should take me a while to get the frame done, so hopefully that'll give everyone who's ripping files from the game more time, cause I'm hoping to get the over armor to be the X-01 (since it has the least amount of clipping and has a helmet that can most easily be modified to not clip into the back when it opens).
The overarmor will also be vacuum formed and then bolted onto the frame.