zyote
Active Member
Hello.
I just started getting into prop building a month or so ago after the purchase of 2 original props from the movie. A Prometheus Ampule, and a very larger and heavy Life Pod Display Panel. (has a 26” LCD screen in it!)
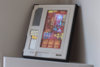
Anyway, I have zero experience making props, never built anything, or know how to even drill straight holes, i went about learning a few basics to get started on a small scale version of this big panel. I figured if i mentally took the big panel apart. i could tackle each problem a lot easier. I decided to use base my scale off of an iPhone/iPod Touch screen. As i figured that’s how the graphics would most easily be displayed.
1. Made some measurements off the large panel, and worked it up into multiple pieces in Illustrator. I would be sending these files off to a local laser cutting place to be cut into white acrylic. I was told by a friend who works on films, that these sort of panels are typically made this way, i.e. laser cut and sandwiched together. He also suggested acrylic as a good medium to use. rather than wood.
Here are the various pieces i drew up:
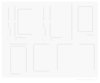
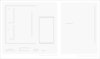
I had 4 different Acrylic thicknesses available to me, so i just picked a few as starting points. my depth measurements haven’t been too accurate yet, as i’m still trying to figure out how it all fits together, and covers over the iPhone’s bulk. In fact i had to extend the height of the panel a little more than the original in order to cover the top piece fully. Perhaps one day i can figure out how to do this sort of thing with off-the-shelf LCD displays. But that would involve a lot of lessons in electronics.
A few days later i received my laser cut pieces in the mail, i weeded off the excess backing sheet to better show the parts:
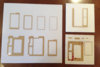
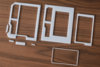
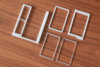
I did a number of different width pieces because i’ve never done laser cutting, or know how detailed acrylic can be cut without it breaking before, and so i figured this would be my test set. Surprisingly to me, it can be very thin indeed! the cuts are really good!
I’ve also realized that most of these parts are too thick (depth wise), and so i’ll probably need to pick a smaller size for my next order. I’ve also tried laying out where the phone will slot into the thickest part (the back piece). I don’t think this will be the direction i’ll go, because i need to have the phone’s display much higher up to the front. and the bulk of this piece i think is gonna be problematic.
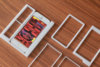
For the lower side ‘button panel’ i want to backlight it underneath a film/transparency of some kind. I also am still trying to figure out what type of plastic i need. And especially how i can print on it, and have the light shine through it. My first thought was to try printing with my home epson workforce wf-7510 (pigment based inks) onto an Inkjet Back Lit Film from Papilio (Inkjet Back-Lit Film), the film hasn’t arrived yet, but if it doesn’t work out, i may need to get this printed properly elsewhere. In the meantime, i’ve printed placeholder displays + fake metal mesh (for the top left area) out on glossy paper. Just to get a feel for the sizing:
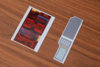
If the Papilio back lit film does work, then my original intention was to back light it with a tiny EL sheet. However, after speaking to my prop-making friend, he suggested i should side light it with LEDs through some frosted clear acrylic, suggesting that it gives a better look that isn’t quite so harsh. He suggested i try LED tape lighting:
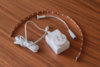
Given the size/scale of this project, i’d probably only need a 1/4 of that length. And secondly, i have no idea yet how i can mount this in such a small space. I would also have to figuring out a way to cut the power cables down to a better size, or switch to battery power. Basically, i’m concerned about the bulk of this. I really didn’t want there to much in the way of cables + power etc on a project this small.
Here is all the laser cut acrylic pieces, sitting (unglued) on top of the iPhone display, and the printed button panel. It looks pretty good if i do say so myself! (i do!).:
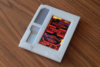
I am also thinking of purchasing a Graphtec CE6000-40 cutting machine for cutting the little vinyl lettering and stuff. (I also want to use it for other projects too! like making stickers, signs, etc). So have been learning about vinyl a lot as well.
But this really is just the beginning. Lots to redo, lots of lesson’s to be learned. I wanted to share this here on this forum to keep me motivated, and to get feedback on the direction i’m taking it, the methods i’m using, and hopefully it’s a project you’re interested in seeing too.
Current Questions i’d love advice on:
1. What type of film/transparency/plastic can i get printed so it looks awesome under backlighting? I’m happy to pay a professional company to do it, i just need to know what to ask for! Any URLs or Businesses very much appreciated.
2. What are your thoughts on my LED tape lighting direction? is there something better suited for this scale?
3. Where can i get a mini hexagonal metal grid mesh from? i need it to be micro scale!
THANKS!!
Mischa
I just started getting into prop building a month or so ago after the purchase of 2 original props from the movie. A Prometheus Ampule, and a very larger and heavy Life Pod Display Panel. (has a 26” LCD screen in it!)
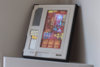
Anyway, I have zero experience making props, never built anything, or know how to even drill straight holes, i went about learning a few basics to get started on a small scale version of this big panel. I figured if i mentally took the big panel apart. i could tackle each problem a lot easier. I decided to use base my scale off of an iPhone/iPod Touch screen. As i figured that’s how the graphics would most easily be displayed.
1. Made some measurements off the large panel, and worked it up into multiple pieces in Illustrator. I would be sending these files off to a local laser cutting place to be cut into white acrylic. I was told by a friend who works on films, that these sort of panels are typically made this way, i.e. laser cut and sandwiched together. He also suggested acrylic as a good medium to use. rather than wood.
Here are the various pieces i drew up:
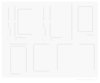
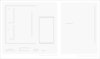
I had 4 different Acrylic thicknesses available to me, so i just picked a few as starting points. my depth measurements haven’t been too accurate yet, as i’m still trying to figure out how it all fits together, and covers over the iPhone’s bulk. In fact i had to extend the height of the panel a little more than the original in order to cover the top piece fully. Perhaps one day i can figure out how to do this sort of thing with off-the-shelf LCD displays. But that would involve a lot of lessons in electronics.
A few days later i received my laser cut pieces in the mail, i weeded off the excess backing sheet to better show the parts:
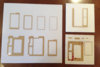
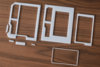
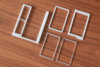
I did a number of different width pieces because i’ve never done laser cutting, or know how detailed acrylic can be cut without it breaking before, and so i figured this would be my test set. Surprisingly to me, it can be very thin indeed! the cuts are really good!
I’ve also realized that most of these parts are too thick (depth wise), and so i’ll probably need to pick a smaller size for my next order. I’ve also tried laying out where the phone will slot into the thickest part (the back piece). I don’t think this will be the direction i’ll go, because i need to have the phone’s display much higher up to the front. and the bulk of this piece i think is gonna be problematic.
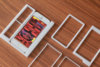
For the lower side ‘button panel’ i want to backlight it underneath a film/transparency of some kind. I also am still trying to figure out what type of plastic i need. And especially how i can print on it, and have the light shine through it. My first thought was to try printing with my home epson workforce wf-7510 (pigment based inks) onto an Inkjet Back Lit Film from Papilio (Inkjet Back-Lit Film), the film hasn’t arrived yet, but if it doesn’t work out, i may need to get this printed properly elsewhere. In the meantime, i’ve printed placeholder displays + fake metal mesh (for the top left area) out on glossy paper. Just to get a feel for the sizing:
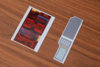
If the Papilio back lit film does work, then my original intention was to back light it with a tiny EL sheet. However, after speaking to my prop-making friend, he suggested i should side light it with LEDs through some frosted clear acrylic, suggesting that it gives a better look that isn’t quite so harsh. He suggested i try LED tape lighting:
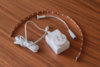
Given the size/scale of this project, i’d probably only need a 1/4 of that length. And secondly, i have no idea yet how i can mount this in such a small space. I would also have to figuring out a way to cut the power cables down to a better size, or switch to battery power. Basically, i’m concerned about the bulk of this. I really didn’t want there to much in the way of cables + power etc on a project this small.
Here is all the laser cut acrylic pieces, sitting (unglued) on top of the iPhone display, and the printed button panel. It looks pretty good if i do say so myself! (i do!).:
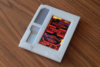
I am also thinking of purchasing a Graphtec CE6000-40 cutting machine for cutting the little vinyl lettering and stuff. (I also want to use it for other projects too! like making stickers, signs, etc). So have been learning about vinyl a lot as well.
But this really is just the beginning. Lots to redo, lots of lesson’s to be learned. I wanted to share this here on this forum to keep me motivated, and to get feedback on the direction i’m taking it, the methods i’m using, and hopefully it’s a project you’re interested in seeing too.
Current Questions i’d love advice on:
1. What type of film/transparency/plastic can i get printed so it looks awesome under backlighting? I’m happy to pay a professional company to do it, i just need to know what to ask for! Any URLs or Businesses very much appreciated.
2. What are your thoughts on my LED tape lighting direction? is there something better suited for this scale?
3. Where can i get a mini hexagonal metal grid mesh from? i need it to be micro scale!
THANKS!!
Mischa