OK guys - well I finally got the Captain America helmet finished (well almost - just some air brushing to finish).
So I documented the process mostly to try to get some feedback and to share my "lessons learnt"
So after cutting out the paper pattern and transferring it to the foam, I had the basic shapes to start working with.
First lesson was to keep the knife straight. I had some odd angles to work with while gluing that I had to try to change after the event (I didn't keep the knife straight while cutting so I had to straighten some of the edges with the dremel before gluing). Having already started my next project, I have since gone out and bought a hot knife - makes it a whole heap easier to cut straight edges.
Next was the gluing and putting it all together
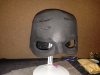
Second lesson learnt here was to take your time holding the joins together. Some went together nicely and others didn't - they left reasonable size gaps. I used hot glue also and it was quite messy to work with (leaving stringy bits and it cools quickly). I am still using it for this next project but I might give superglue a go somewhere along the line.
As the gaps were a bit of a pain, I decided to use this helmet as a bit of a trial and error process. Also, don't use a hotgun over your piece after the gluing - I learnt that the hard way - it pulls the joins apart and they are harder to work back together.
To fill the gaps where the joins weren't great, I decided to try 2 different methods - I filled one side and the eyes with paintable silicone. On the other side I used the hot glue to fill the gaps, pushed the gaps together a bit more and then sanded it back with the dremel (by the way, if you aren't using a dremel during this, you are doing it wrong - it's a god send) Below is the work in progress image. Left side (white colour) is the silicone. Right side is the glue.
The silicone went on and spread easily, however following the drying process it sank a little into the gap. You would have to put a few layers on to get it to smooth out. I used water to smooth it out (on the tip of one of my fingers) as well as a scraper to see what worked and what didn't. Both pretty much yielded the same results but the water process ensure a very level and smooth finish.
The glue levelled out OK with the sanding and it felt pretty smooth. But until you paint you can't really see the results.
So after applying the gap fillers the process was as follows:
1. 2 coats of PVA glue (around a 50/50 consistency
2. 3 coats of Plastidip
3. 1 coat of Grey Enamel primer
4. 2 coats of the Blue Enamel
5. 2 coats of airbrushed acrylic for the logos.
The results are as follows:
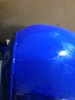
You may not be able to see it in the pictures but the silicone was a much better result (picture on the left). If you spent the time adding the silicone into the gaps to smooth it out you should get a pretty good finish. The glue, as I said before, felt and looked OK after applying and sanding, but the end results were really rough and stood out much more.
So the almost finished result:
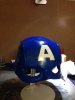
The final lesson to be learnt here is the tape that I used to shape the A. I used painting tape (like you would when painting walls etc) to restrict the airbrushing, but after peeling it off it seems to have left some marks - more like removed some of the shine around the A. I'll have to look for another option next I head into the Hardware store.
Overall though, good fun and am well on my way to making the next one. For someone who has only made the plastic scale models before, I'm really getting into this and enjoying every minute.
EDIT:
Final result
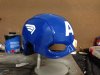
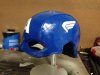