Lutso
Sr Member
Hey guys. Sorry if this is a little off-kilter for the RPF, but I would rather ask questions about fabricating from the folks here than on the gun boards.
(If this sort of thing is not allowed, mods feel free to remove with notification).
I have a Modern 12ga. scatter gun that I am converting into a WWII-style trench gun. I am modeling it off the Winchester 1912 for reference. So far I've got all stock and body parts covered, and it is really looking good. However, it's time for me to start thinking about adding the iconic heat shield to the barrel...and there in lies my trouble.
I simply will not settle for the heat shields that are currently sold to work with modern shotguns, as they look like crap and are not of the right length or fitment for what I want.
Here is what I am trying to replicate (shield section only - not the bayo lug):
Since I will not shell out 30-60$ on a stock shroud that I don't even like to begin with, I've started entertaining the idea of fabbing it.
Keep in mind this thread is only concerned with the perforated (shroud) portions of the assembly.
I have two ideas;
My first option is to buy a sheet of perforated steel or aluminum, cut it to desired length and width, and roll it into a half-tube to sit atop the barrel. However, purchasing cuts of perf sheet from vendors such as onlinemetals.com will leave me with unfinished edges (i.e., partially-cut holes creating "bumps" along the permeter of the sheet). I can't have this. There needs to be a smooth margin around the perimeter of the piece for this to work.
My other idea was to get a length of perforated tubing and simply cut it in half length-wise. However, this poses the same problem as the first in that I will inevitably be left with rough edges and partial holes as the perf pattern will not line up.
Not seeing a way to get around these problems, I came up with a design for a custom piece of metal (measurements are rough until I can get some accurate measurements from the gun); a piece of steel or aluminum 14" long and 3" wide, with 3/8" perforations, staggered, with a safety margin of 1/16" along all edges.
However all the prices I've found so far to get this made have proven to be an absolute fortune. I thought it seemed like an easy enough thing to make, but I guess not.
What do you guys think I should do? How would you tackle this if you were in my situation?
(If this sort of thing is not allowed, mods feel free to remove with notification).
I have a Modern 12ga. scatter gun that I am converting into a WWII-style trench gun. I am modeling it off the Winchester 1912 for reference. So far I've got all stock and body parts covered, and it is really looking good. However, it's time for me to start thinking about adding the iconic heat shield to the barrel...and there in lies my trouble.
I simply will not settle for the heat shields that are currently sold to work with modern shotguns, as they look like crap and are not of the right length or fitment for what I want.
Here is what I am trying to replicate (shield section only - not the bayo lug):
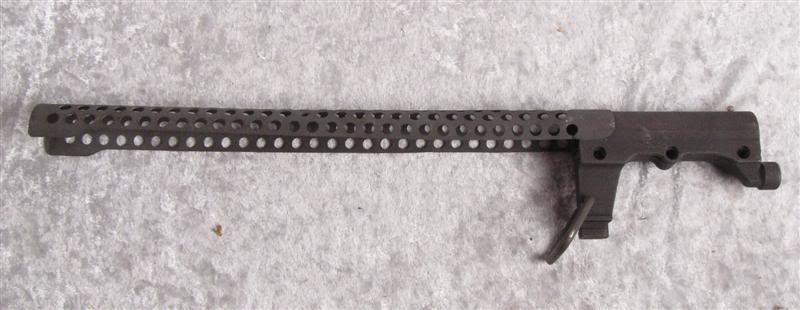
Since I will not shell out 30-60$ on a stock shroud that I don't even like to begin with, I've started entertaining the idea of fabbing it.
Keep in mind this thread is only concerned with the perforated (shroud) portions of the assembly.
I have two ideas;
My first option is to buy a sheet of perforated steel or aluminum, cut it to desired length and width, and roll it into a half-tube to sit atop the barrel. However, purchasing cuts of perf sheet from vendors such as onlinemetals.com will leave me with unfinished edges (i.e., partially-cut holes creating "bumps" along the permeter of the sheet). I can't have this. There needs to be a smooth margin around the perimeter of the piece for this to work.
My other idea was to get a length of perforated tubing and simply cut it in half length-wise. However, this poses the same problem as the first in that I will inevitably be left with rough edges and partial holes as the perf pattern will not line up.
Not seeing a way to get around these problems, I came up with a design for a custom piece of metal (measurements are rough until I can get some accurate measurements from the gun); a piece of steel or aluminum 14" long and 3" wide, with 3/8" perforations, staggered, with a safety margin of 1/16" along all edges.
However all the prices I've found so far to get this made have proven to be an absolute fortune. I thought it seemed like an easy enough thing to make, but I guess not.
What do you guys think I should do? How would you tackle this if you were in my situation?