BRDencklau
Well-Known Member
I started a work in progress thread for a Borderlands 2 themed prop. More of a barge into Prop-dom than a well thought out execution. Needless to say I learned more than I produced a finished product.
And the birds go tweet.
I acquired a copy of Charles Adams: Model Design & Blueprinting Handbook Vol.1 and after re-acquainting myself the the process of orthographic projection and scaling, I couldn't help but see the glaring flaws in my previous endeavor. I shelved the prior project and set out to make a nice collection of workable drawings utilizing the in-game inventory viewing option. I didn't have any examples of the specific weapon I want to reproduce so I utilized three different versions of the Maliwan SMG to get the proper organization of parts. If my math is right, there are 125 different versions of SMGs offered by each of the five weapons manufacturers in the game excluding elemental additions. That's a total of 625 different standard damage sub-machine gun BODIES in game. (The actual amount of smg's based on stats is nearly limitless, but that's not why we are here.)
From these drawings, I made a set of templates and started cutting out the forms. I used standard MDF in 1/2" and 5/8" thickness.
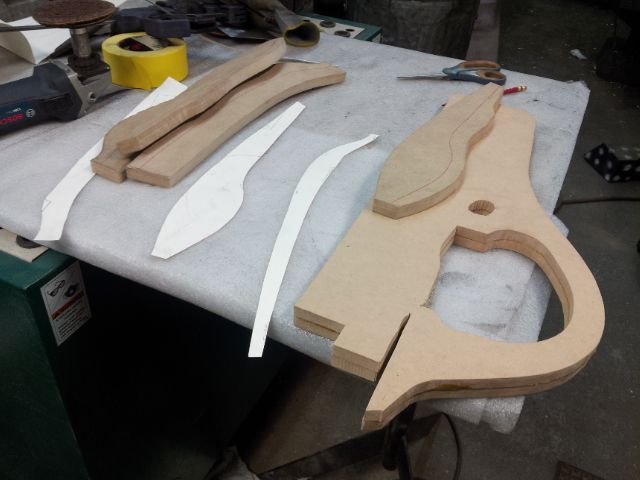
Here is the first set of components mocked up. So far so good.

From my own experience with the forms and reading others efforts, I chose to allow room for the barrel assemblies and sighting components from the start, incorporating space into the stock cutouts.
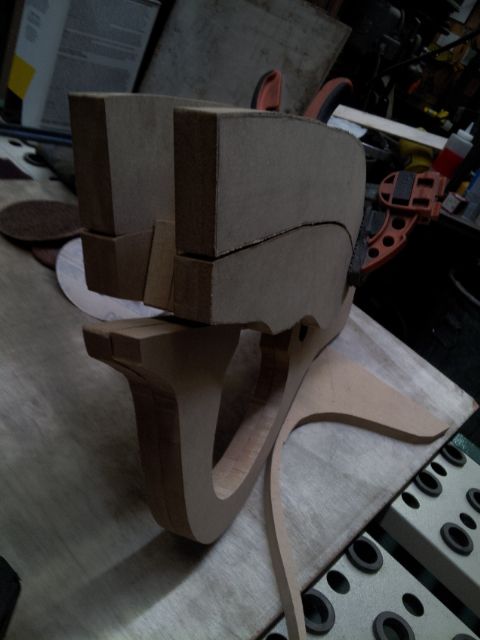
After some basic assembly and shaping techniques, the top of the prop is starting to look good.
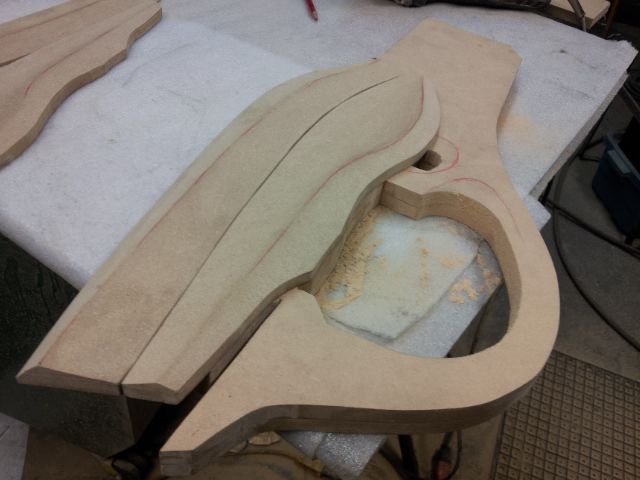
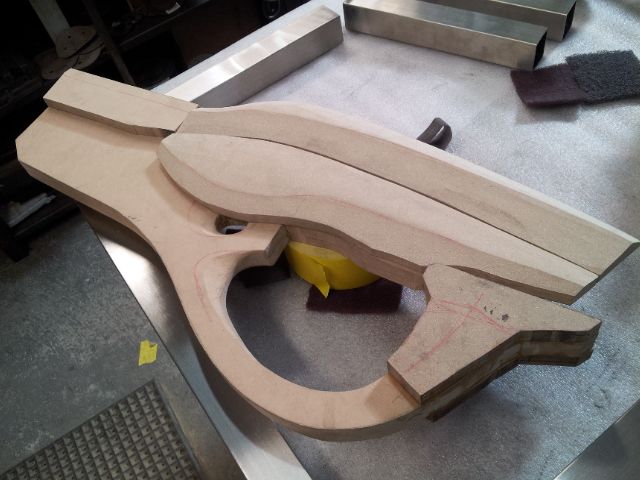
Good drawings are a cornerstone to quick and proper execution. I templated the lower half of the stock/grip and started roughing in the form. Almost all sanding, up to this point, has been done with an angle grinder set up with a sanding backer/60 grit.
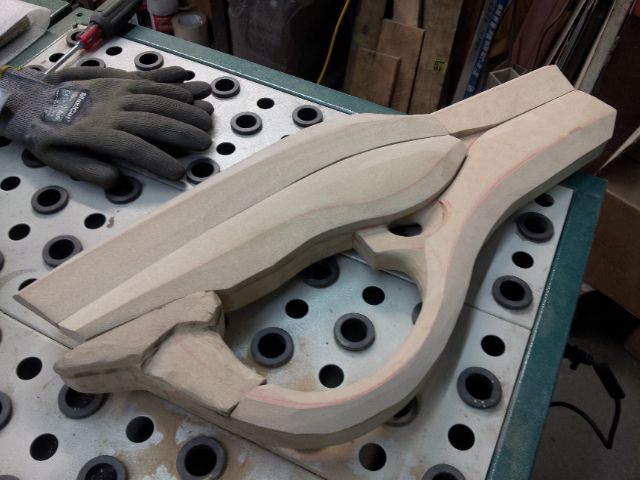
Smoothed out with an orbital sander, the relief components lose dimension in this photo.
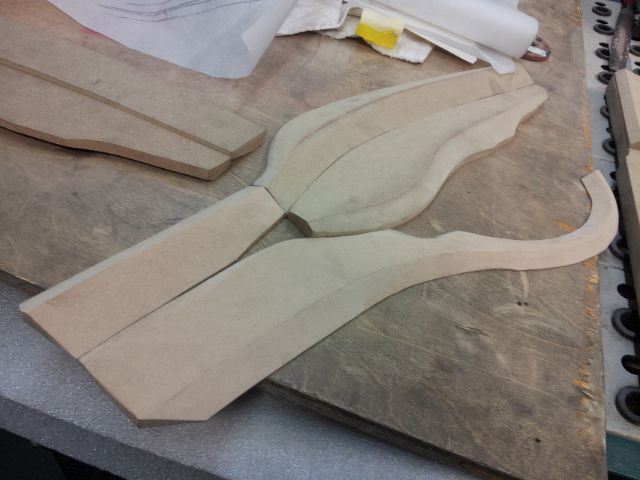
Layout of the magazine cavity. As you can see a good set of scale-able drawings is paramount.

Fine tuned.
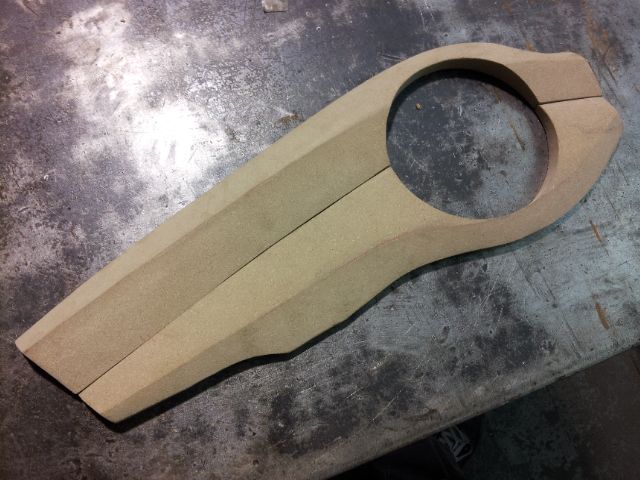
This is how I left it yesterday. More work to come next week.

And the birds go tweet.
I acquired a copy of Charles Adams: Model Design & Blueprinting Handbook Vol.1 and after re-acquainting myself the the process of orthographic projection and scaling, I couldn't help but see the glaring flaws in my previous endeavor. I shelved the prior project and set out to make a nice collection of workable drawings utilizing the in-game inventory viewing option. I didn't have any examples of the specific weapon I want to reproduce so I utilized three different versions of the Maliwan SMG to get the proper organization of parts. If my math is right, there are 125 different versions of SMGs offered by each of the five weapons manufacturers in the game excluding elemental additions. That's a total of 625 different standard damage sub-machine gun BODIES in game. (The actual amount of smg's based on stats is nearly limitless, but that's not why we are here.)
From these drawings, I made a set of templates and started cutting out the forms. I used standard MDF in 1/2" and 5/8" thickness.
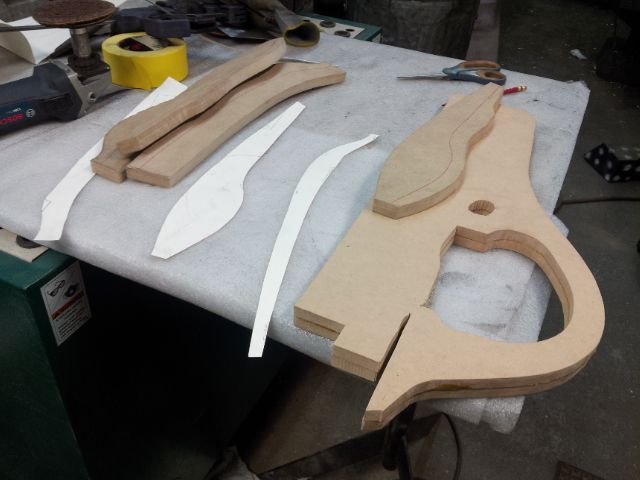
Here is the first set of components mocked up. So far so good.

From my own experience with the forms and reading others efforts, I chose to allow room for the barrel assemblies and sighting components from the start, incorporating space into the stock cutouts.
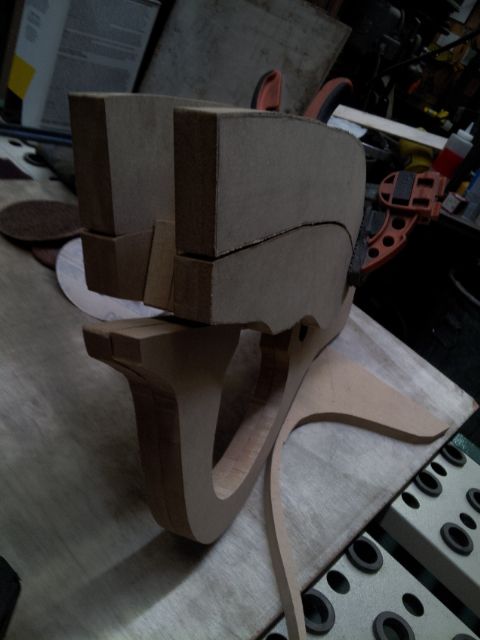
After some basic assembly and shaping techniques, the top of the prop is starting to look good.
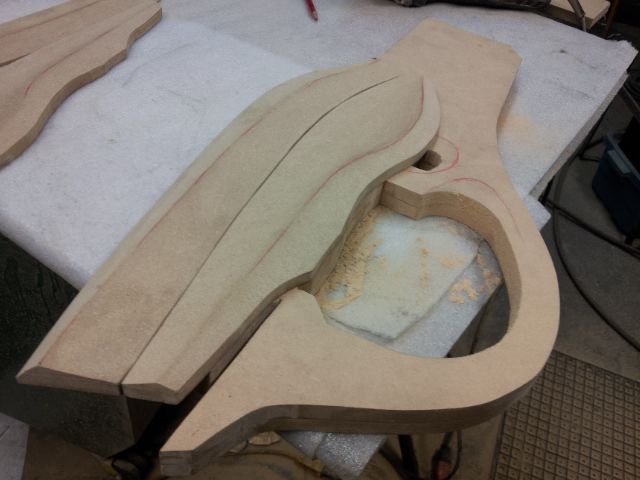
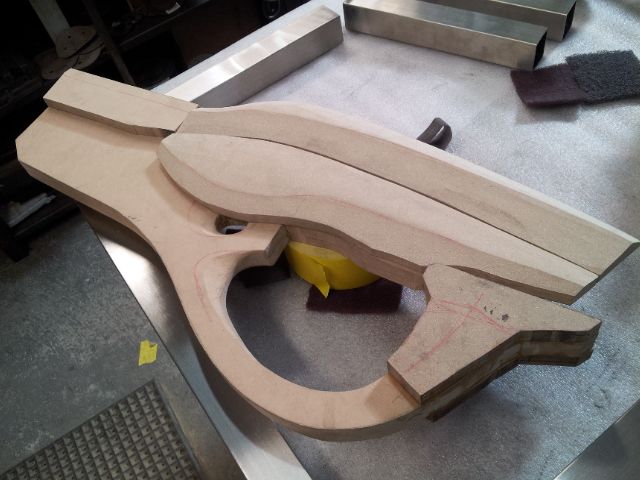
Good drawings are a cornerstone to quick and proper execution. I templated the lower half of the stock/grip and started roughing in the form. Almost all sanding, up to this point, has been done with an angle grinder set up with a sanding backer/60 grit.
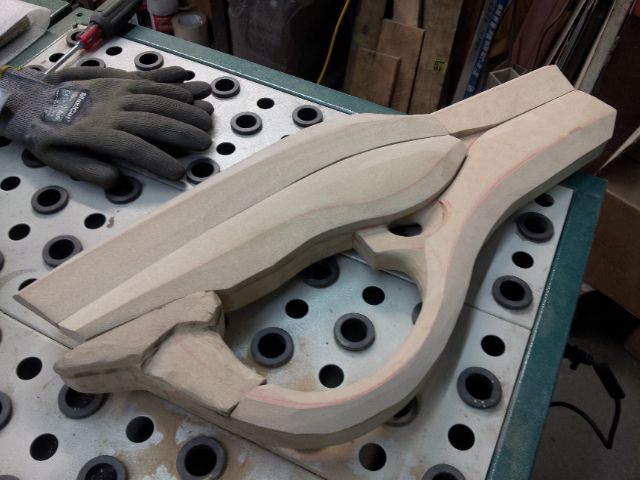
Smoothed out with an orbital sander, the relief components lose dimension in this photo.
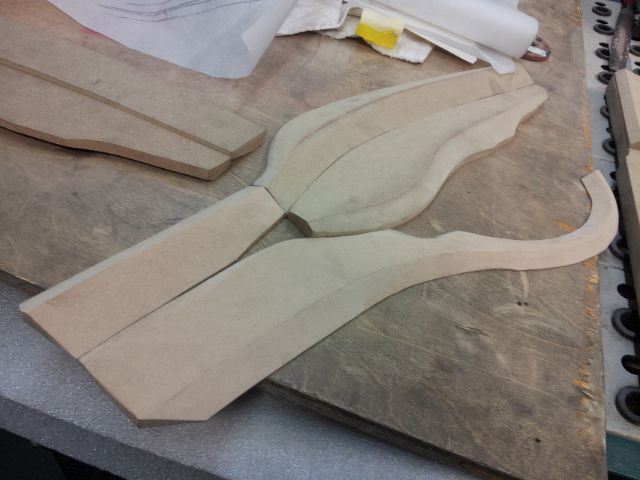
Layout of the magazine cavity. As you can see a good set of scale-able drawings is paramount.

Fine tuned.
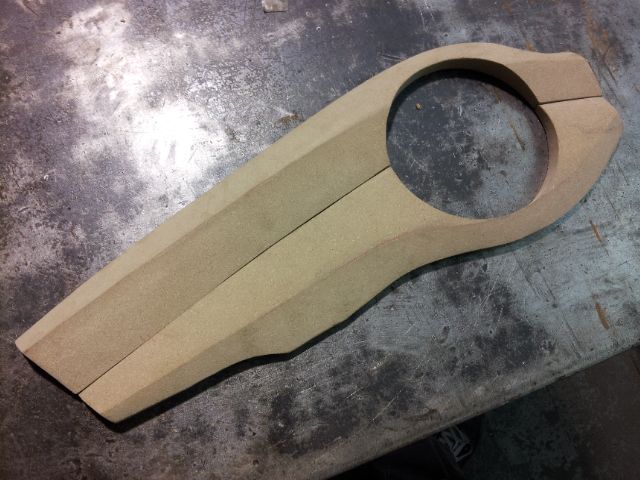
This is how I left it yesterday. More work to come next week.
