mdb
Sr Member
I normally don't enter contests but hey, why not 
This costume was a blend of two that I was working on this year and I am still debating on whether to keep the armour as it is or get the Blood Dragon painted on. And I also am not sure if I will make Nyreen, though the tunic option is kind of appealing right now after two weekends in a row of crowds and armour and a big gun....


*
This page is divided into the different componants:
mask / bodysuit / armour / weapon
Mask.
Sculpting
I sculpted this all in grey plasticine on a foam wig head. I went through a few full head sculpts before finding the right balance between features and that also would fit over my own (there were a lot of.. calibrations). While these photos look much the same there was about a pound of clay removed and added each night to change the proportions. It went through a 'cat' like phase and a 'Planet of the Apes' type phase until I was finally happy with the general look.
After this point I then cut the pieces apart so that I could make the mask in 6 parts total to allow for some movement of the jaw and to allow for some airflow between layers (I've been glued in to asari headpieces and lekku and montral and it is a bit of a drain on health over time.) This was easily the toughest part to get over, as I would essentially destroy my sculpt if anything went wrong.
I cut the mandibles off first and transfered them to a flat sheet of plastic. Then the face was smoothed again and a new mouth line created. Then finally the jaw was removed and transfered to another wig head and reshaped.
Once the shapes were as I wanted I oiled and built walls on the clay ready to cast.
Casting
This was in Ultracal as it gels as it cures which means you can build 3D molds. I made sure the mold was at least an inch thick all over. Once the molds were cured I then removed the wig heads (destroying them in the process by the highly efficient method of stabbing with a large screwdriver and levering the polystryrene out.
Unfortunately the clay proved difficult to remove from the scalp mold- this is due to me wiping too much excess oil off. This necessitates the use of the screwdriver to remove as much clay as possible as well as finger nails (which proved the most effective if not the most painful method). Finally acetone and a toothbrush was used to remove the last of the residue of clay.
Casting
This was a tricky process! I needed to thicken the latex so that it would sta on the walls of the mold- slumping is a problem when trying to get a decent layer when the curing rate would vary day by day. If you do too thin a wall that layer will cure and shrink, then the next layer will cure and shrink further creating warping.
What made this task even more difficult was a bad batch of latex (cry! 5L of product wasted) due to it getting too cold either at the warehouse or shipping to NZ or by courier within NZ. I have no idea at what stage this was but I had it confirmed that this is a very big problem when buying the stuff in NZ. Freight often gets cold even before it reaches our shores.
What this resulted in was the latex gelling and not creating stretchy bonds- it cured and cracked as it shrank. I wound up buying pre-thickened latex and tinting it with acrylic. This worked well and I finally had a good cast.
Below are the bad casts showing warping and cracking.
Below are the paler tinted pieces I wound up with.
Painting
I used a base layer of a mix of Latona's and other alcohol activated paints. First a flat pale grey then a wash of maroon and another layer of white to define the lines and facets of the face.
I then misted a mix of yellow and raw sienna airbrush ink (acrylic) over the pieces.
Assembly
The pieces need to be held in place somehow so I created a fabric hood that I latexed over which it was stretched on a form. The skull cap and facial pieces are then velcro dotted in place as the glue on the back of these bond extremely well with latex- I had to use alcohol to clean paint off the scull cap to allow the glue to adhere.
In the days before I debuted the costume I decided to make my pieces match the armour more- I had used an interference violet pigment powder to give an added element of light over the flat pieces of the armour (first colour in the first image below). So I used the interference green with pale yellow over the forehead and flanges of the face and mixed interference blue with a pale pink over the jaw, cheeks, mandibles skull cap and hood (neck). I then defined the bumps on the skull cap and the scales down the back with the same yellow mix.
Bodysuit
This was first drawn out on a test suit with enough panels already cut and sewn to be able to cope with even more seams added. I wound up transfering the pattern to card then deciding to scrap it and try for a pattern that actually could be taken in easily as adding in the extra seams and thus seam allowances caused the pattern to get larger.
While the photos below show the final pattern they are on a low stretch silver vinyl- I discarded several fabrics while cretaing this suit before deciding to stick with stretch PVC as it has body and support and with seams it looks in world and practical rather than just super shiny
I overlocked the seams by home machine then industrial. Until I broke a needle and decided to not replace it. Rimoldi make great machines but this one was not built with the user in mind- the screw for the needles requires an allen key and is difficult to get to. Rethreading is incredibly difficult too.
Finally I had to put elastic straps at the feet to hold the lower legs tight and to cover the top of the foot.
Armour
Patterning
I first test drove a papercraft pattern available online but I made it too large and it was slightly asymmetric. I then would up using a few shapes as a guide (collars, back pack, shoulder points and knees) then using backing paper to pattern everything else by wrapping my mannequin in it and drawing over it. Then there were at least two card tests made before the final pattern was developed (all those pieces are in red).
In order to get a good pattern I first reshaped my mannequin...
Cutting and tooling
I traced around the pattern pieces in black ink and then cut each piece out with a swivel knife, beveling tool and scissors. The leather was damp as if were tooling (just enough to change the colour of the surface permanently but not wet) and then details were likewise tooled with swivel knife and beveling tool. The texture was added using a texture tool and also a wire wastebasket hammered into the surface.
The pieces were then soaked in cold water for at least 24 hours and shaped over PVC pipe and other forms.
Gluing
I used a water based contact adhesive to laminate the formed pieces to another vege tanned leather (cured so not able to be shaped- instead I added darts and seams where needed.) The shoes were additionally held together with Shoe Goo.
Dyeing and finishing
I dyed the outside and inside of each piece with Feibing dye, which is alcohol diluted. To both seal and condition the leather I used Rub 'n' Buff in Silver Leaf to polish the outside of all pieces. This whole suit used two and a half tubes. I squeezed the polish in to a shallow dish and applied the polish with some faux suede- this allowed a wide surface area to be applied at a time.
To properly seal the leather I also used Resolene. I applied it plain over the mesh texture and then mixed in interference violet pigment powder to seal the smooth surfaces. This creates a shifting purple glow over some pieces, adding extra interest.
Rigging
I used rivets of varying depths to create articulated joints and wide textured elastic to hold the hips, thighs and upper arms in place. It also is used on the knee pieces. I also cut slits in the armour harness and threaded non roll elastic through with suspender clasps on the ends to grip to the shoulder pieces and keep them in place. I also used satchel latches to hold the front chest to the back. Velcro was also used to hold this in place as well as the greaves. The gauntlets were riveted to the elbow cops and a width of leather holds the upper inside in place. The rigidity of the leather keeps the lower part of the gauntlets in place.
Black Widow rifle
This was fibreglass over foam core card stock- as used by architects et al.I used cardboard tubes and pvc pip for the interior of the scope and rifle ends. The stock and butt are made from laminated foam core carved to shape and fibreglassed.
And finally:
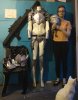
Bad camera photo is bad.. but I really need an extra set of hands to get in to the costume and yet another to take the photo! My new hipster glasses, and obligatory cat who helps as all cats help, and the last remnants of pink hair....
And more progress on my site:
turian « Search Results « The Plain Jane Costume Chronicles
So I started this November 8/9 last year!
nyreen « Search Results « The Plain Jane Costume Chronicles
(For some reason these results in particular are out of order.....)
blood dragon « Search Results « The Plain Jane Costume Chronicles
femshep « Search Results « The Plain Jane Costume Chronicles
And the two threads here:
http://www.therpf.com/f24/blood-dragon-femshep-leather-armour-m98-aka-big-gun-page-2-a-190280/
(armour, bodysuit and gun)
http://www.therpf.com/f24/wip-female-turian-s-nyreen-neimhaille-174192/
(I started making Nyreen, got distracted and will paint up another set from my molds to be Nyreen)
This costume was a blend of two that I was working on this year and I am still debating on whether to keep the armour as it is or get the Blood Dragon painted on. And I also am not sure if I will make Nyreen, though the tunic option is kind of appealing right now after two weekends in a row of crowds and armour and a big gun....








This page is divided into the different componants:
mask / bodysuit / armour / weapon
Mask.
Sculpting
I sculpted this all in grey plasticine on a foam wig head. I went through a few full head sculpts before finding the right balance between features and that also would fit over my own (there were a lot of.. calibrations). While these photos look much the same there was about a pound of clay removed and added each night to change the proportions. It went through a 'cat' like phase and a 'Planet of the Apes' type phase until I was finally happy with the general look.






After this point I then cut the pieces apart so that I could make the mask in 6 parts total to allow for some movement of the jaw and to allow for some airflow between layers (I've been glued in to asari headpieces and lekku and montral and it is a bit of a drain on health over time.) This was easily the toughest part to get over, as I would essentially destroy my sculpt if anything went wrong.
I cut the mandibles off first and transfered them to a flat sheet of plastic. Then the face was smoothed again and a new mouth line created. Then finally the jaw was removed and transfered to another wig head and reshaped.











Once the shapes were as I wanted I oiled and built walls on the clay ready to cast.




Casting
This was in Ultracal as it gels as it cures which means you can build 3D molds. I made sure the mold was at least an inch thick all over. Once the molds were cured I then removed the wig heads (destroying them in the process by the highly efficient method of stabbing with a large screwdriver and levering the polystryrene out.
Unfortunately the clay proved difficult to remove from the scalp mold- this is due to me wiping too much excess oil off. This necessitates the use of the screwdriver to remove as much clay as possible as well as finger nails (which proved the most effective if not the most painful method). Finally acetone and a toothbrush was used to remove the last of the residue of clay.










Casting
This was a tricky process! I needed to thicken the latex so that it would sta on the walls of the mold- slumping is a problem when trying to get a decent layer when the curing rate would vary day by day. If you do too thin a wall that layer will cure and shrink, then the next layer will cure and shrink further creating warping.
What made this task even more difficult was a bad batch of latex (cry! 5L of product wasted) due to it getting too cold either at the warehouse or shipping to NZ or by courier within NZ. I have no idea at what stage this was but I had it confirmed that this is a very big problem when buying the stuff in NZ. Freight often gets cold even before it reaches our shores.
What this resulted in was the latex gelling and not creating stretchy bonds- it cured and cracked as it shrank. I wound up buying pre-thickened latex and tinting it with acrylic. This worked well and I finally had a good cast.


Below are the bad casts showing warping and cracking.





Below are the paler tinted pieces I wound up with.


Painting
I used a base layer of a mix of Latona's and other alcohol activated paints. First a flat pale grey then a wash of maroon and another layer of white to define the lines and facets of the face.


I then misted a mix of yellow and raw sienna airbrush ink (acrylic) over the pieces.

Assembly
The pieces need to be held in place somehow so I created a fabric hood that I latexed over which it was stretched on a form. The skull cap and facial pieces are then velcro dotted in place as the glue on the back of these bond extremely well with latex- I had to use alcohol to clean paint off the scull cap to allow the glue to adhere.


In the days before I debuted the costume I decided to make my pieces match the armour more- I had used an interference violet pigment powder to give an added element of light over the flat pieces of the armour (first colour in the first image below). So I used the interference green with pale yellow over the forehead and flanges of the face and mixed interference blue with a pale pink over the jaw, cheeks, mandibles skull cap and hood (neck). I then defined the bumps on the skull cap and the scales down the back with the same yellow mix.


Bodysuit
This was first drawn out on a test suit with enough panels already cut and sewn to be able to cope with even more seams added. I wound up transfering the pattern to card then deciding to scrap it and try for a pattern that actually could be taken in easily as adding in the extra seams and thus seam allowances caused the pattern to get larger.



While the photos below show the final pattern they are on a low stretch silver vinyl- I discarded several fabrics while cretaing this suit before deciding to stick with stretch PVC as it has body and support and with seams it looks in world and practical rather than just super shiny


I overlocked the seams by home machine then industrial. Until I broke a needle and decided to not replace it. Rimoldi make great machines but this one was not built with the user in mind- the screw for the needles requires an allen key and is difficult to get to. Rethreading is incredibly difficult too.



Finally I had to put elastic straps at the feet to hold the lower legs tight and to cover the top of the foot.
Armour
Patterning
I first test drove a papercraft pattern available online but I made it too large and it was slightly asymmetric. I then would up using a few shapes as a guide (collars, back pack, shoulder points and knees) then using backing paper to pattern everything else by wrapping my mannequin in it and drawing over it. Then there were at least two card tests made before the final pattern was developed (all those pieces are in red).
In order to get a good pattern I first reshaped my mannequin...












Cutting and tooling
I traced around the pattern pieces in black ink and then cut each piece out with a swivel knife, beveling tool and scissors. The leather was damp as if were tooling (just enough to change the colour of the surface permanently but not wet) and then details were likewise tooled with swivel knife and beveling tool. The texture was added using a texture tool and also a wire wastebasket hammered into the surface.
The pieces were then soaked in cold water for at least 24 hours and shaped over PVC pipe and other forms.

















Gluing
I used a water based contact adhesive to laminate the formed pieces to another vege tanned leather (cured so not able to be shaped- instead I added darts and seams where needed.) The shoes were additionally held together with Shoe Goo.



Dyeing and finishing
I dyed the outside and inside of each piece with Feibing dye, which is alcohol diluted. To both seal and condition the leather I used Rub 'n' Buff in Silver Leaf to polish the outside of all pieces. This whole suit used two and a half tubes. I squeezed the polish in to a shallow dish and applied the polish with some faux suede- this allowed a wide surface area to be applied at a time.
To properly seal the leather I also used Resolene. I applied it plain over the mesh texture and then mixed in interference violet pigment powder to seal the smooth surfaces. This creates a shifting purple glow over some pieces, adding extra interest.




Rigging
I used rivets of varying depths to create articulated joints and wide textured elastic to hold the hips, thighs and upper arms in place. It also is used on the knee pieces. I also cut slits in the armour harness and threaded non roll elastic through with suspender clasps on the ends to grip to the shoulder pieces and keep them in place. I also used satchel latches to hold the front chest to the back. Velcro was also used to hold this in place as well as the greaves. The gauntlets were riveted to the elbow cops and a width of leather holds the upper inside in place. The rigidity of the leather keeps the lower part of the gauntlets in place.

Black Widow rifle
This was fibreglass over foam core card stock- as used by architects et al.I used cardboard tubes and pvc pip for the interior of the scope and rifle ends. The stock and butt are made from laminated foam core carved to shape and fibreglassed.








And finally:
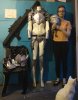
Bad camera photo is bad.. but I really need an extra set of hands to get in to the costume and yet another to take the photo! My new hipster glasses, and obligatory cat who helps as all cats help, and the last remnants of pink hair....
And more progress on my site:
turian « Search Results « The Plain Jane Costume Chronicles
So I started this November 8/9 last year!
nyreen « Search Results « The Plain Jane Costume Chronicles
(For some reason these results in particular are out of order.....)
blood dragon « Search Results « The Plain Jane Costume Chronicles
femshep « Search Results « The Plain Jane Costume Chronicles
And the two threads here:
http://www.therpf.com/f24/blood-dragon-femshep-leather-armour-m98-aka-big-gun-page-2-a-190280/
(armour, bodysuit and gun)
http://www.therpf.com/f24/wip-female-turian-s-nyreen-neimhaille-174192/
(I started making Nyreen, got distracted and will paint up another set from my molds to be Nyreen)