Yodajammies
Sr Member
EvilFx got me hooked on EVA foam, and I had planned on building a Mass Effect suit for this year's DragonCon, so I figured I would need a nice weapon to go along with it.
I commissioned a 3d model from Vrogy (not sure if he is a member here). It's actually the assault rifle from Mass Effect I. The M8 is the rifle from the sequel and has a couple slight design changes, but I digress.
The cylindrical bits of this rifle are laser cut acrylic rings that are threaded onto a dowel. The barrels I'm trying to commission out so that I'm not forced to use this same technique.
First pass on the shopbot. This model was milled from 10lb/ft^3 density tooling board.
Second pass
After milling both sides, seaming them together, sealing, and giving them a protective acrylic coat, we then come to the scrap molding.
After 3 coats of OOMOO. I'm not sure I particularly care for this brand of silicone. I think I should have gone with Mold Max or just spent the money and used Rebound 25.
Cylindrical greeble that goes on the right side of the rifle.
I should have the mold done and ready to pull a cast by the end of the weekend. *crosses fingers*
I commissioned a 3d model from Vrogy (not sure if he is a member here). It's actually the assault rifle from Mass Effect I. The M8 is the rifle from the sequel and has a couple slight design changes, but I digress.
The cylindrical bits of this rifle are laser cut acrylic rings that are threaded onto a dowel. The barrels I'm trying to commission out so that I'm not forced to use this same technique.
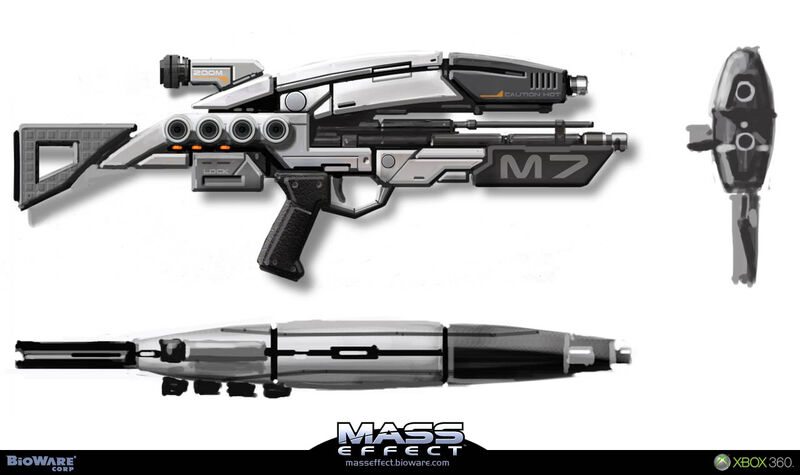

First pass on the shopbot. This model was milled from 10lb/ft^3 density tooling board.

Second pass

After milling both sides, seaming them together, sealing, and giving them a protective acrylic coat, we then come to the scrap molding.

After 3 coats of OOMOO. I'm not sure I particularly care for this brand of silicone. I think I should have gone with Mold Max or just spent the money and used Rebound 25.

Cylindrical greeble that goes on the right side of the rifle.

I should have the mold done and ready to pull a cast by the end of the weekend. *crosses fingers*