Cobheran
New Member
I started playing League of Legends recently and decided that I really wanted to make Ashe's bow. I used her splash artwork for the main bow design and the in game model for the smaller designs.
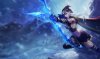
I made the model in Rhino 4 and exported it as a .stl file so the CAM program can translate it into code for the CNC.
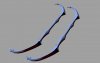
I imported the .stl model into my CAM program and converted it into lines of code. The red lines are supports to keep the bow from dislodging from the wood before the mill is done cutting it out.
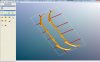
The model is converted into movement code, each line is represented as a line. The green blob is actually half a million lines of code.

The code is moved to the mill computer. The model is replaced with the lines of movement that the mill will take to create the model.
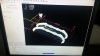
Since I don't know of anywhere locally that sells 1.25" MDF, I use 3/4" and 1/2" boards and glue them together
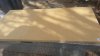
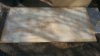
I use clamps to pinch the wood together and stand it upright to keep the edges even.
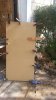
I mount the boards on the mill and drill them into the spoil board to prevent the mill from moving the wood around while it's cutting.
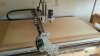
First rough cut on the mill! This is a cut designed to clear away material before a detail pass later on
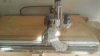
Detail pass making things pretty!
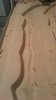
After the finishing passes I remove the board from the mill and cut away the supporting flashing and material
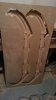
I use a belt sander to sand the back of the bow until the flashing is gone and it lines up perfectly!
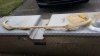
I had a few pieces of wood not adhere well and lost them, so I'll have to sculpt/re-cut those pieces individually. After sanding I'll prime the bow to correct errors, then smooth it out to a glass finish. Then I'm planning on making a matrix mold (which I may need some advice on since I've never actually done one) and casting the bow in Smooth-On's Crystal Clear 200. Let me know what you guys think!
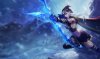
I made the model in Rhino 4 and exported it as a .stl file so the CAM program can translate it into code for the CNC.
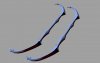
I imported the .stl model into my CAM program and converted it into lines of code. The red lines are supports to keep the bow from dislodging from the wood before the mill is done cutting it out.
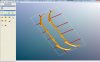
The model is converted into movement code, each line is represented as a line. The green blob is actually half a million lines of code.

The code is moved to the mill computer. The model is replaced with the lines of movement that the mill will take to create the model.
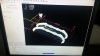
Since I don't know of anywhere locally that sells 1.25" MDF, I use 3/4" and 1/2" boards and glue them together
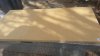
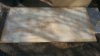
I use clamps to pinch the wood together and stand it upright to keep the edges even.
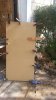
I mount the boards on the mill and drill them into the spoil board to prevent the mill from moving the wood around while it's cutting.
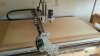
First rough cut on the mill! This is a cut designed to clear away material before a detail pass later on
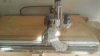
Detail pass making things pretty!
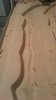
After the finishing passes I remove the board from the mill and cut away the supporting flashing and material
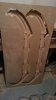
I use a belt sander to sand the back of the bow until the flashing is gone and it lines up perfectly!
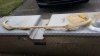
I had a few pieces of wood not adhere well and lost them, so I'll have to sculpt/re-cut those pieces individually. After sanding I'll prime the bow to correct errors, then smooth it out to a glass finish. Then I'm planning on making a matrix mold (which I may need some advice on since I've never actually done one) and casting the bow in Smooth-On's Crystal Clear 200. Let me know what you guys think!