holtt
Active Member
I want to cast a part in resin that has indented letters which will be filled with paint - exactly like the kind of thing you see on old meters like the one below...
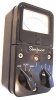
In fact what I want to do is cast a new front panel for that same meter, but with different lettering.
Does anyone have any advice on exactly how to do that in a very clear and crisp way? I could certainly create a master and use letter punches to create indented letters, but I imagine the consistency of imprint depth as well as letter alignment won't be perfect unless I come up with some kind of jig and device.
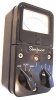
In fact what I want to do is cast a new front panel for that same meter, but with different lettering.
Does anyone have any advice on exactly how to do that in a very clear and crisp way? I could certainly create a master and use letter punches to create indented letters, but I imagine the consistency of imprint depth as well as letter alignment won't be perfect unless I come up with some kind of jig and device.