Hi RPfer's
Sometime ago I purchased a BvS Dawn of Justice Armoured Batsuit Helmet from TheRocketeer - I'm not sure if that particular thread is still current in the project runs forum, but I can certainly recommend therocketeer's products and customer service. The helmet is a work of art.
http://www.therpf.com/showthread.php?t=242962
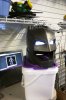
The initial plan was just to have the helmet as a display piece - but as other members of this forum detailed their suit builds using EVA foam I decided to try building one myself. This idea was only reinforced after seeing the movie and how imposing and awesome the mecha suit looked.
I bought Aztlans patterns and thought this looks do-able. Despite practicing with some EVA foam pieces before committing to a build, purchasing and reading Bill Doran's books as well as purchasing and watching Stealth from Heroes Workshop videos along with watching Evil Ted Smith's YouTube videos - I still couldn't get my cuts straight enough nor my seams smooth enough nor get the patterns scaled right.
Looking at the revisions IM Nation did to his build, he mentioned that he got some components from Do3D,
http://www.therpf.com/showthread.php?t=244404
I checked out their site and the penny dropped - they make 3d models for 3d printers, I have a 3d printer !
http://do3d.com/product/3d-printable-batman-suit-bvs/
A few emails latter, a funds transaction and some down loading later it's time to get busy.
I had initially planned to do a build log - but found there were not enough hours in the day to go to work, fabricate the suit, get on with my life and write a build log. So what I thought I would do is now that the build is finished I'd write some thoughts and reflections here in following posts to maybe help others who are interested in following this route to make a costume.
Chris
Sometime ago I purchased a BvS Dawn of Justice Armoured Batsuit Helmet from TheRocketeer - I'm not sure if that particular thread is still current in the project runs forum, but I can certainly recommend therocketeer's products and customer service. The helmet is a work of art.
http://www.therpf.com/showthread.php?t=242962
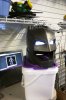
The initial plan was just to have the helmet as a display piece - but as other members of this forum detailed their suit builds using EVA foam I decided to try building one myself. This idea was only reinforced after seeing the movie and how imposing and awesome the mecha suit looked.
I bought Aztlans patterns and thought this looks do-able. Despite practicing with some EVA foam pieces before committing to a build, purchasing and reading Bill Doran's books as well as purchasing and watching Stealth from Heroes Workshop videos along with watching Evil Ted Smith's YouTube videos - I still couldn't get my cuts straight enough nor my seams smooth enough nor get the patterns scaled right.
Looking at the revisions IM Nation did to his build, he mentioned that he got some components from Do3D,
http://www.therpf.com/showthread.php?t=244404
I checked out their site and the penny dropped - they make 3d models for 3d printers, I have a 3d printer !
http://do3d.com/product/3d-printable-batman-suit-bvs/
A few emails latter, a funds transaction and some down loading later it's time to get busy.
I had initially planned to do a build log - but found there were not enough hours in the day to go to work, fabricate the suit, get on with my life and write a build log. So what I thought I would do is now that the build is finished I'd write some thoughts and reflections here in following posts to maybe help others who are interested in following this route to make a costume.
Chris
Last edited: