Thought I would share some initial and early progress on my ‘5 foot’ Millennium Falcon dimensional survey and eventual studio scale build.
I come from a Visual Effects/Design Engineering background and I’ll be leveraging techniques and tools I use every day to help define the forms and overall dimensions of the model – as an initial first step.
I decided to start with the ‘core shape’ – the forms that have no kit-bashed or scratch-built parts.
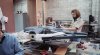
The next step was to analyze the image and strategically define converging perspective lines to estimate the ‘camera lens - field of view’.
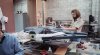
By defining the lens ‘field of view’ and later establish some base-line dimensions of key forms, one can infer other details and start to build additional core shapes.
At this point, I had to make a few assumptions and begin the process.
For example, I felt safe in assuming that the docking hatch and gun turret forms were symmetrical in the X and Y-axis, respectively. In other words, the docking hatches are mirrored along the X-axis and the gun turret forms are mirrored along the Y-axis across a central origin buried in the middle of the model’s armature.
I also referenced my old Star Wars sketchbook and noted the 2” diameter shaft call out on the gun turret Falcon sketches and worked out that the permanent sleeve shaft diameters are probably 2.25” (1/8” wall thickness). For the model mover shaft, they most likely used a 2” diameter steel shaft and an ID collet chuck to affix the model to said 2” shaft.
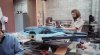
One of my first design engineering jobs in visual effects was at Boss Film Studios working for Richard Edlund and the model mover shafts there were often of the same configuration.
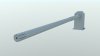
By breaking down the major mechanical shapes and assign those variables with assumed values, I derived other dimensional forms and measurements for my initial mock-up.
Further, based on very detailed and researched information posted on this forum (i.e. 3” mandible hole diameters, 2” mandible thickness in the Y axis etc.) I arrived at an initial form guesstimate:
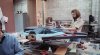
I even found a vintage Travel Lodge Motel Room glass on a certain Internet auction site and decided to use it as additional dimensional cross-reference – my humble contribution to the studio-scale pantheon of reference objects:
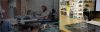
After a fair amount of time researching, making assumptions, modeling, cross-referencing and estimating…
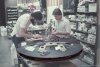
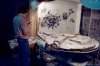
Parts of it seem to be lining up – other areas…not so much.
I then decided to grab a short image sequence from Star Wars (ep IV) and track the MF in 3D as it escapes the Death Star. I wanted to see how my initial assumption would compare against the studio-scale model in an actual shot from the film.
escapeTheDeathStar 001 on Vimeo
Encouraging - but too soon to call it solved. I decided to try a slightly different tack.
More to follow...
Regards,
Andre
I come from a Visual Effects/Design Engineering background and I’ll be leveraging techniques and tools I use every day to help define the forms and overall dimensions of the model – as an initial first step.
I decided to start with the ‘core shape’ – the forms that have no kit-bashed or scratch-built parts.
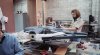
The next step was to analyze the image and strategically define converging perspective lines to estimate the ‘camera lens - field of view’.
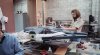
By defining the lens ‘field of view’ and later establish some base-line dimensions of key forms, one can infer other details and start to build additional core shapes.
At this point, I had to make a few assumptions and begin the process.
For example, I felt safe in assuming that the docking hatch and gun turret forms were symmetrical in the X and Y-axis, respectively. In other words, the docking hatches are mirrored along the X-axis and the gun turret forms are mirrored along the Y-axis across a central origin buried in the middle of the model’s armature.
I also referenced my old Star Wars sketchbook and noted the 2” diameter shaft call out on the gun turret Falcon sketches and worked out that the permanent sleeve shaft diameters are probably 2.25” (1/8” wall thickness). For the model mover shaft, they most likely used a 2” diameter steel shaft and an ID collet chuck to affix the model to said 2” shaft.
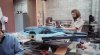
One of my first design engineering jobs in visual effects was at Boss Film Studios working for Richard Edlund and the model mover shafts there were often of the same configuration.
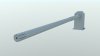
By breaking down the major mechanical shapes and assign those variables with assumed values, I derived other dimensional forms and measurements for my initial mock-up.
Further, based on very detailed and researched information posted on this forum (i.e. 3” mandible hole diameters, 2” mandible thickness in the Y axis etc.) I arrived at an initial form guesstimate:
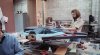
I even found a vintage Travel Lodge Motel Room glass on a certain Internet auction site and decided to use it as additional dimensional cross-reference – my humble contribution to the studio-scale pantheon of reference objects:
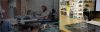
After a fair amount of time researching, making assumptions, modeling, cross-referencing and estimating…
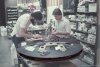
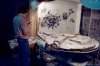
Parts of it seem to be lining up – other areas…not so much.
I then decided to grab a short image sequence from Star Wars (ep IV) and track the MF in 3D as it escapes the Death Star. I wanted to see how my initial assumption would compare against the studio-scale model in an actual shot from the film.
escapeTheDeathStar 001 on Vimeo
Encouraging - but too soon to call it solved. I decided to try a slightly different tack.
More to follow...
Regards,
Andre