Yodajammies
Sr Member
Well, since I'm solidly into molding this fella and there's very little chance of me NOT finishing it (knock on wood), I figure its time to start my build thread.
I took a stab at hand sculpting/casting this sword, but I vastly misjudged the thickness of the handle and ended up with a lump of unusable plastic. On the bright side it was definitely good practice for sculpting symmetry, so there is that...
So now "taking the easy route" / "cheating" as some call it, I had a 3d model built by our own Vrogy (http://www.flickr.com/photos/vrogy), who did a lovely job of digitally sculpting this blade. I took his high poly model into Rhino and chopped it up into a bunch of unrecognizable pieces to skirt the Shapeways "no weapons" policy, though you could argue this is merely a prop anyway.
Shapeways delivers!
Now comes the fun part: Sanding. Since this blade is so thin yet has raised details, the stair stepping effect from printing is very noticeable in places. This nylon material ("Strong, flexible, white") is quite resilient too. You really have to use some elbow grease to cut into the groves on these parts, and its highly unlikey that you'll OVERsand.
Fast-forward through the boring parts.......
Primed and ready for molding!
I'll be pouring up the second half of the mold tonight, and should have a test cast out of the mold sometime later this week. Huzzah!
These blades will be cast in EpoxaCast 690 using PearlEx and So-Strong powder/liquid pigment tints. I've pretty much got the mix down, but I may tweak it a bit more depending on how the first couple casts come out.
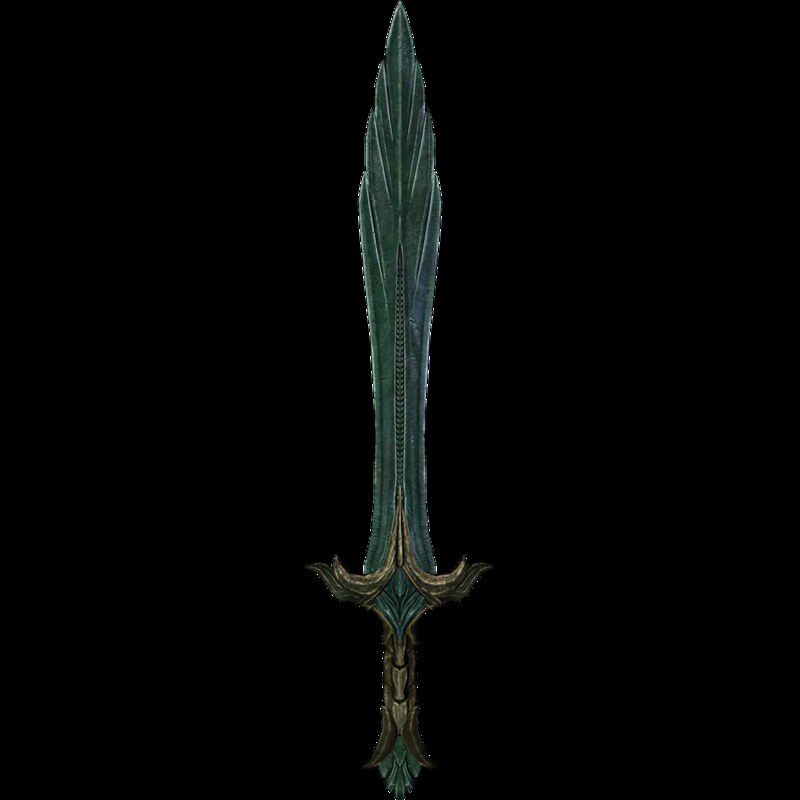
I took a stab at hand sculpting/casting this sword, but I vastly misjudged the thickness of the handle and ended up with a lump of unusable plastic. On the bright side it was definitely good practice for sculpting symmetry, so there is that...

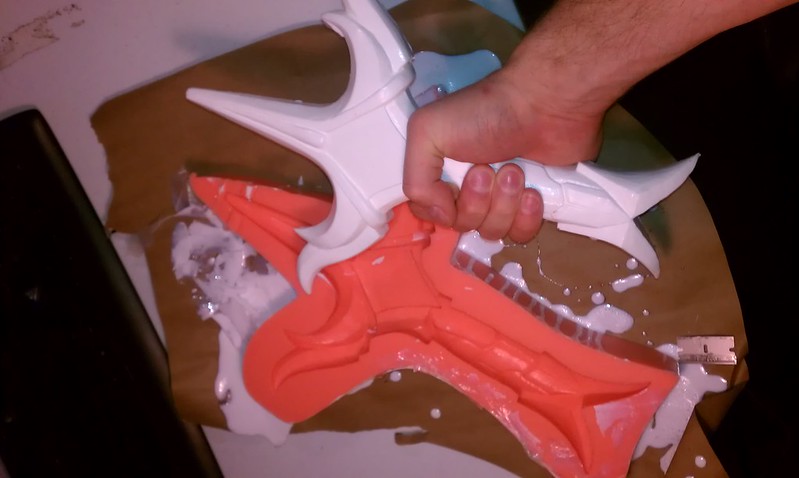
So now "taking the easy route" / "cheating" as some call it, I had a 3d model built by our own Vrogy (http://www.flickr.com/photos/vrogy), who did a lovely job of digitally sculpting this blade. I took his high poly model into Rhino and chopped it up into a bunch of unrecognizable pieces to skirt the Shapeways "no weapons" policy, though you could argue this is merely a prop anyway.


Shapeways delivers!
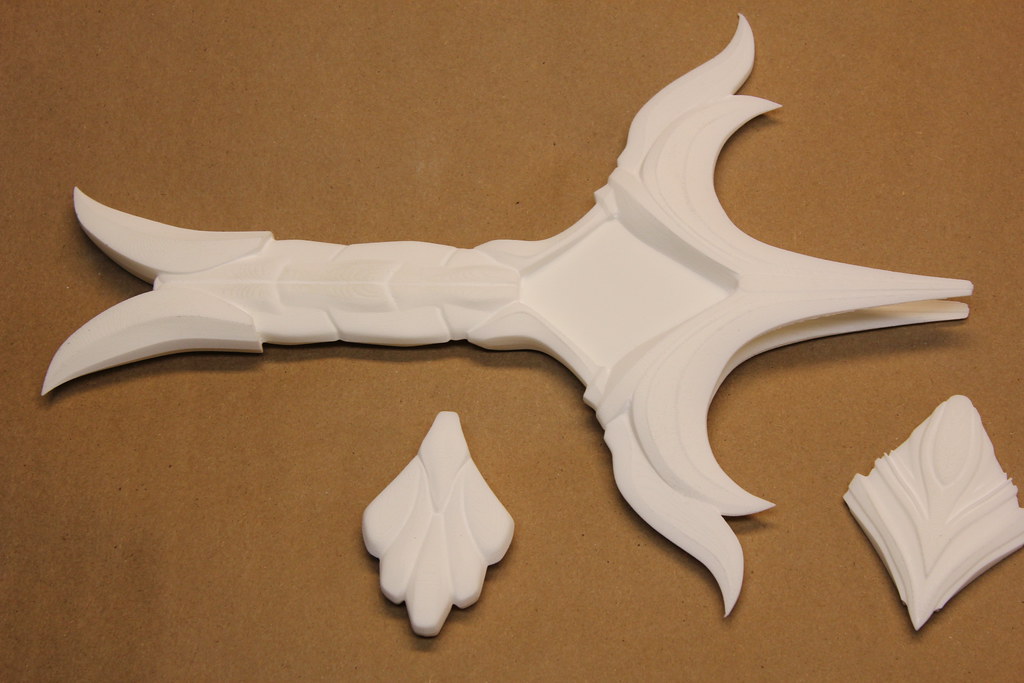

Now comes the fun part: Sanding. Since this blade is so thin yet has raised details, the stair stepping effect from printing is very noticeable in places. This nylon material ("Strong, flexible, white") is quite resilient too. You really have to use some elbow grease to cut into the groves on these parts, and its highly unlikey that you'll OVERsand.

Fast-forward through the boring parts.......
Primed and ready for molding!
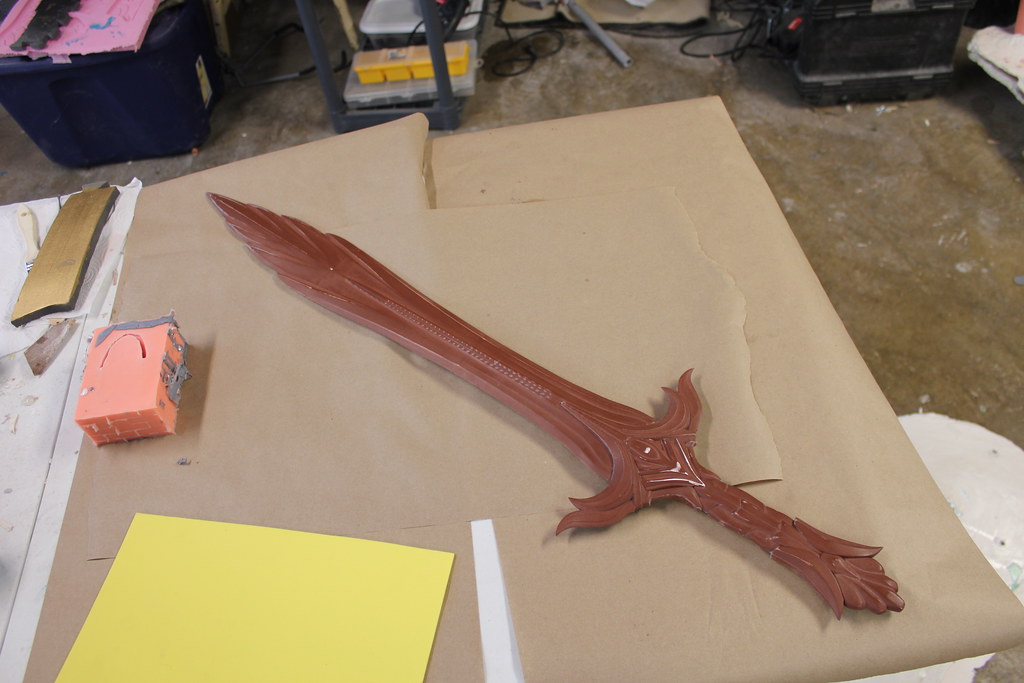

I'll be pouring up the second half of the mold tonight, and should have a test cast out of the mold sometime later this week. Huzzah!
These blades will be cast in EpoxaCast 690 using PearlEx and So-Strong powder/liquid pigment tints. I've pretty much got the mix down, but I may tweak it a bit more depending on how the first couple casts come out.
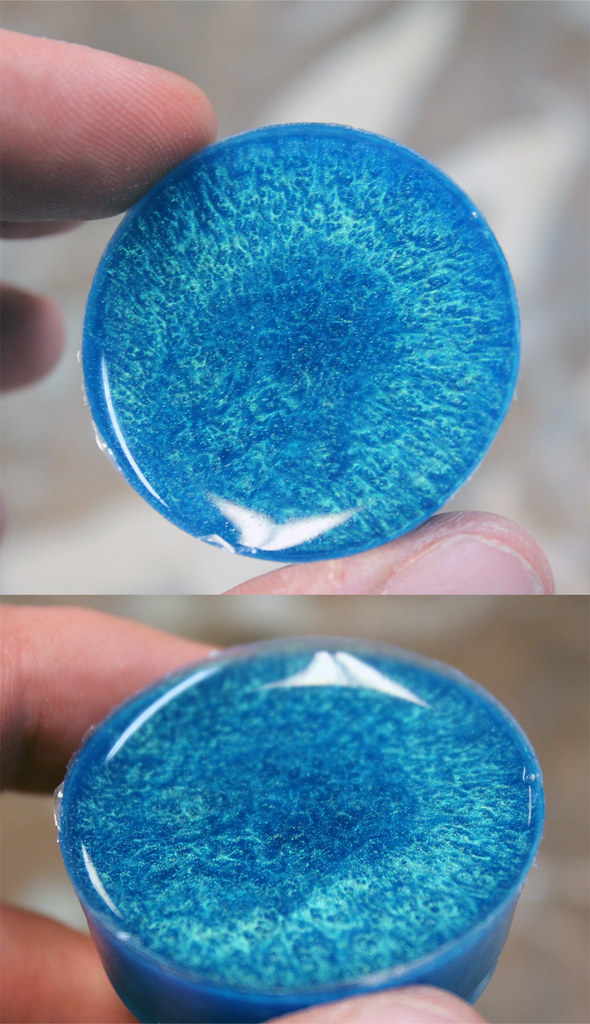
Attachments
Last edited: