TheC0lonel
New Member
Hi guys!
So, about a week ago, I finished up a pretty decent Kylo Ren sculpt.
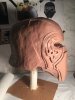
It's slightly rough, but my first time creating a scupt of that complexity, so I decided to mold it and cast in resin, then sand out any imperfections. Today, I de-molded it for the first time.
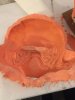
It came out exactly how I wanted - no tears, no inhibition, nothing apparently wrong except for one thing:
The mold won't fit back on.
Specifically, when I put the mold back on the sculpt, there's about a quarter inch of flex in certain areas. It looks like some of the undercuts won't fit back into the cavities on the sculpture. I'm kind of worried about this.
Has anyone encountered this problem before? Can it be fixed? If it can't be fixed, what's the worst-case scenario?
EDIT:
Okay, I fixed the problem. Here's a tip: first of all, never do what I did. Apparently, I read a really bad tutorial.
However, if this does happen to you, cover the stuck parts of the mold with water and dish soap. Then push. It works!
So, about a week ago, I finished up a pretty decent Kylo Ren sculpt.
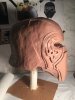
It's slightly rough, but my first time creating a scupt of that complexity, so I decided to mold it and cast in resin, then sand out any imperfections. Today, I de-molded it for the first time.
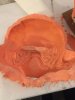
It came out exactly how I wanted - no tears, no inhibition, nothing apparently wrong except for one thing:
The mold won't fit back on.
Specifically, when I put the mold back on the sculpt, there's about a quarter inch of flex in certain areas. It looks like some of the undercuts won't fit back into the cavities on the sculpture. I'm kind of worried about this.
Has anyone encountered this problem before? Can it be fixed? If it can't be fixed, what's the worst-case scenario?
EDIT:
Okay, I fixed the problem. Here's a tip: first of all, never do what I did. Apparently, I read a really bad tutorial.
However, if this does happen to you, cover the stuck parts of the mold with water and dish soap. Then push. It works!
Last edited: