Wreckhur
Jr Member
I am currently building a fully functioning X-files alien stiletto. It is double action out the front, spring operated. For safety and legal reasons, I have designed two safeties into this project. The first is a weakened carbon fiber blade, that will break with enough force applied. It requires only a few pounds to do this. Secondly, I have designed a fail safe in the secondary lock, that if the blade is not defeated, it will automatically return inside the handle to prevent injury. Now that the legal stuff is out of the way...
I have about 180 hours invested in the blueprints, mock up and two prototypes. The only real reason for this, has been with the relatively small dimensions and the complexity of the mechanism. I have consulted several fellow machinists during this process and we have all agreed that with a few modifications, my initial design is sound. That being said, I have my own shop, so I can spend as much time as I want on personal projects. :cool
I was initially skeptical about showing the process and progress of my work, as I hope to sell these and I didn't want someone to copy my work... But then I realized, there is no point of me being on this forum, if I don't share my passion and my work. So if people can make this after watching me, GREAT. I will help you every step of the way. (No I won't give you the blueprints :devil.) Anything else though is fair game! I am not going to chronicle my previous versions of this, only this final, complete, working, Alien Stiletto Mk3.
To start with here are the machines I am using: a Bridgeport Mill with Acu-rite control center and a Grizzly lathe.
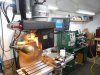
The materials: Starting from the left, 4 small screws that I have to turn down, 4 springs of various size, a .070" X 5" carbon fiber rod, 1" X 10" 6061 round aluminum bar, 5/8" X 8" 6061 square aluminum bar, 1 1/8" X 8 1/2" 8620 round steel bar, 7/16" X 1 1/2" 4140 round steel bar, 1/4" X 1 1/4" X 3 1/2" random plastic and a 1/2" X 1/2" X 1" 4140 flat steel bar.
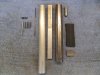
Lathe tools from top left to right: Adjustable angle tool, cut-off tool, custom ground radius tool, 30 degree tool, 1/2" boring bar. Milling tools from bottom left to right: 2 flute 1/4" ball end mill, 3 flute 7/16" end mill, 2 flute 3/32" end mill and my 1 1/2" fly cutter.
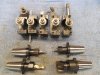
Finally I have my mockup. This is obviously very rough and was only used to proof my concept, it is also much larger and without the safeties of what I will be doing. However, this is the only way to show the process from the inside. The piece on top, is actually on it's side and turned 45 degrees so you can see the channel. If you look closely you can see the spring on the backside. This piece I am calling the "Carriage". The piece laying down, with the channel facing up, I call the "Frame". At the very left of the picture you can see my carbon fiber "Blade" is set into a steel "Blade Holder", this is actually the final "Blade Holder" as the first two iterations I used brass, which galled too easily and kept getting stuck, and a 7075 aluminum "Blade Holder", also galled, thus my settling on the 4140 steel.
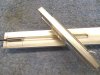
Finally I am not sure how the internal parts will hold up to repeated use, so I may change them after this project is complete and I do some wear testing. Why don't I just change the material now you ask? There are a few reasons. The harder a material is, the longer it takes to machine to the final dimensions, it also wears on tool bits more, weighs more and finally costs more.
I'm not sure if anyone would like to see videos of the machining process. If enough people would like to see some video, I will try my hand at video editing and speed up the process like 4x or maybe more. If anyone has questions, by all means ask away. If there is anything I missed or something you want to see, let me know and I will try my best to make it happen.
I have about 180 hours invested in the blueprints, mock up and two prototypes. The only real reason for this, has been with the relatively small dimensions and the complexity of the mechanism. I have consulted several fellow machinists during this process and we have all agreed that with a few modifications, my initial design is sound. That being said, I have my own shop, so I can spend as much time as I want on personal projects. :cool
I was initially skeptical about showing the process and progress of my work, as I hope to sell these and I didn't want someone to copy my work... But then I realized, there is no point of me being on this forum, if I don't share my passion and my work. So if people can make this after watching me, GREAT. I will help you every step of the way. (No I won't give you the blueprints :devil.) Anything else though is fair game! I am not going to chronicle my previous versions of this, only this final, complete, working, Alien Stiletto Mk3.
To start with here are the machines I am using: a Bridgeport Mill with Acu-rite control center and a Grizzly lathe.
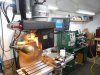
The materials: Starting from the left, 4 small screws that I have to turn down, 4 springs of various size, a .070" X 5" carbon fiber rod, 1" X 10" 6061 round aluminum bar, 5/8" X 8" 6061 square aluminum bar, 1 1/8" X 8 1/2" 8620 round steel bar, 7/16" X 1 1/2" 4140 round steel bar, 1/4" X 1 1/4" X 3 1/2" random plastic and a 1/2" X 1/2" X 1" 4140 flat steel bar.
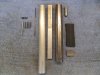
Lathe tools from top left to right: Adjustable angle tool, cut-off tool, custom ground radius tool, 30 degree tool, 1/2" boring bar. Milling tools from bottom left to right: 2 flute 1/4" ball end mill, 3 flute 7/16" end mill, 2 flute 3/32" end mill and my 1 1/2" fly cutter.
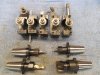
Finally I have my mockup. This is obviously very rough and was only used to proof my concept, it is also much larger and without the safeties of what I will be doing. However, this is the only way to show the process from the inside. The piece on top, is actually on it's side and turned 45 degrees so you can see the channel. If you look closely you can see the spring on the backside. This piece I am calling the "Carriage". The piece laying down, with the channel facing up, I call the "Frame". At the very left of the picture you can see my carbon fiber "Blade" is set into a steel "Blade Holder", this is actually the final "Blade Holder" as the first two iterations I used brass, which galled too easily and kept getting stuck, and a 7075 aluminum "Blade Holder", also galled, thus my settling on the 4140 steel.
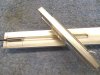
Finally I am not sure how the internal parts will hold up to repeated use, so I may change them after this project is complete and I do some wear testing. Why don't I just change the material now you ask? There are a few reasons. The harder a material is, the longer it takes to machine to the final dimensions, it also wears on tool bits more, weighs more and finally costs more.
I'm not sure if anyone would like to see videos of the machining process. If enough people would like to see some video, I will try my hand at video editing and speed up the process like 4x or maybe more. If anyone has questions, by all means ask away. If there is anything I missed or something you want to see, let me know and I will try my best to make it happen.