Sorry for not having an update recently. Things had been slow going, but are picking up again.
Below is the finished thigh piece (1 of 2). I'm showing different stages of the finishing process, along with some narrative of what occurs at each step. I've also started using a bit of a different technique for finishing the pieces. Here's what I'm doing...
Instead of Bondo, I've decided to use wood filler instead. Bondo is a pain to work with. Not much working time, horrible fumes and it's a pain to sand. I don't need it for strength, I just need it to fill gaps and smooth certain small areas out. So, I decided to try wood filler, and it works great! It has a great working time, is easily applied, no fumes, and can be sanded smooth.
After applying the filler to small gaps and whatnot, I sand it down. Then I apply a coat of resin over the "finished" side of the piece. I then spray it with a filler primer, which helps fill any small problem areas, and shows any other areas that needs more touch-up. Once the "finished" side is complete, I then fiberglass and resin coat the back side of the piece for strength. It's a great process and is helping speed up the finishing process.
Enjoy the pics!
Here's the piece after filling and priming. Just about ready for paint at this step.
Here's the backside of the piece after fiberglass and resin. Super strong after this. I sprayed it because you might be able to see small parts of the back as I walk.
First coat of paint is a "hammered metal" finish. It comes out of a can, has HORRIBLE fumes, but it looks amazing. Makes a great basecoat!
I then airbrush a semi-transparent blue over the piece. This helps show the "cold" of the metal. Remember, this is the Lich King we're dealing with. I may actually add icicles at a later date (there are great products out there to do this)...we'll see how much effort I want to put in!
Gold trim around the edge and I start airbrushing black in the valley's and highlight the peaks with a semi-transparent silver.
Finished piece.
Just a different angle. The paint job shifts colors in the light. Really helps sell the "frozen" part of it. The paint is perfect for this project!
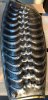