Vrogy
Well-Known Member
Doin' it.
Plan is to cut these with a gazelle or craft robo or CNC laser or something- sure as hell won't be by hand. Then assemble, resin, fiberglass, and a thin layer of paperclay, some hand-carved and cut detail passes, weathering, sealant, paint, straps, leatherwork, etc. Some foam-skinning for the metal trimming, in spots.
Made most of the models

dagonbawn.c4d * by vrogy, on Flickr
Made most of the pep files
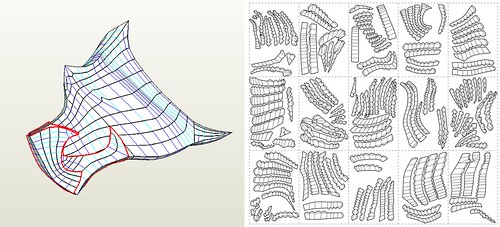
Dragonbone Pauldron in Pepakura by vrogy, on Flickr
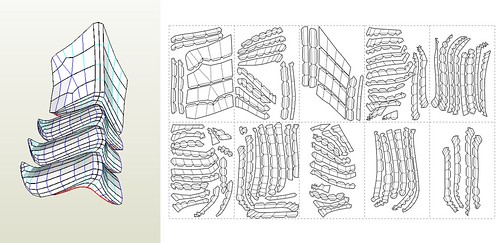
Dragonbone Thigh in Pepakura by vrogy, on Flickr
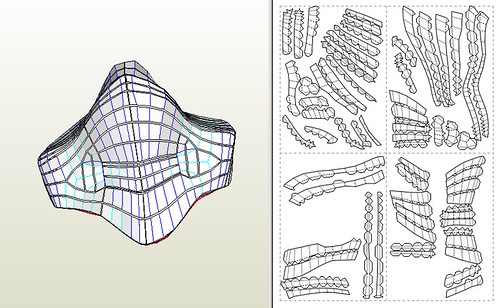
Dragonbone Knee in Pepakura by vrogy, on Flickr
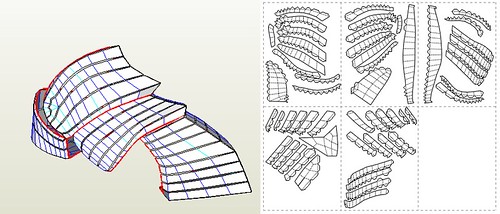
Dragonbone Sabaton in Pepakura by vrogy, on Flickr
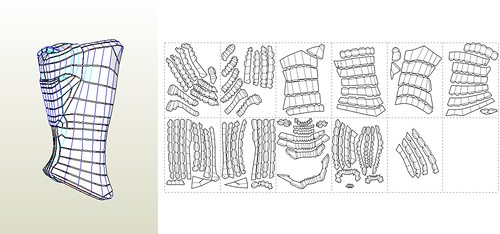
Dragonbone Greave in Pepakura by vrogy, on Flickr
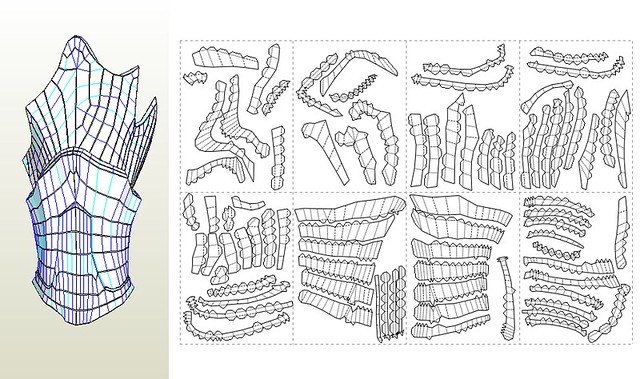
Dragonbone Forearm in Pepakura by vrogy, on Flickr
need to finish models and unfolds, cut, and assemble.
Plan is to cut these with a gazelle or craft robo or CNC laser or something- sure as hell won't be by hand. Then assemble, resin, fiberglass, and a thin layer of paperclay, some hand-carved and cut detail passes, weathering, sealant, paint, straps, leatherwork, etc. Some foam-skinning for the metal trimming, in spots.
Made most of the models

dagonbawn.c4d * by vrogy, on Flickr
Made most of the pep files
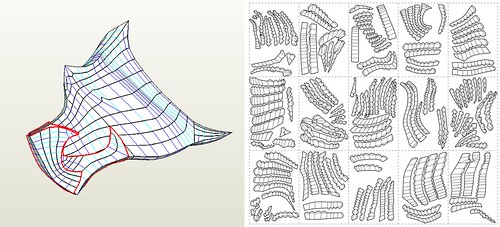
Dragonbone Pauldron in Pepakura by vrogy, on Flickr
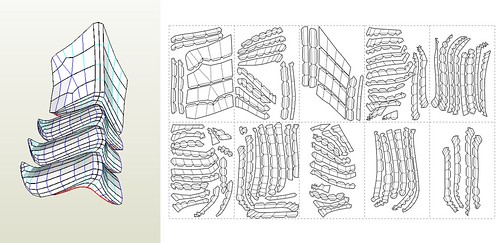
Dragonbone Thigh in Pepakura by vrogy, on Flickr
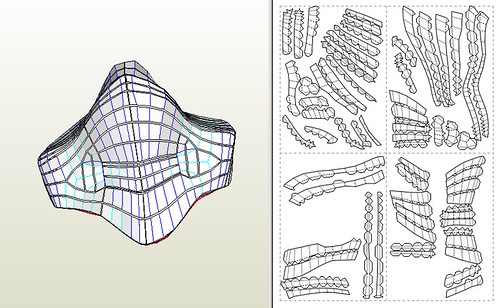
Dragonbone Knee in Pepakura by vrogy, on Flickr
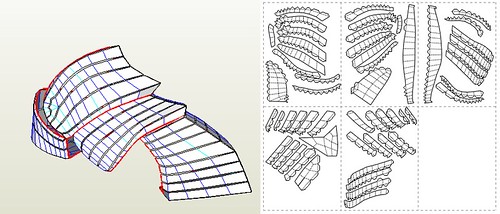
Dragonbone Sabaton in Pepakura by vrogy, on Flickr
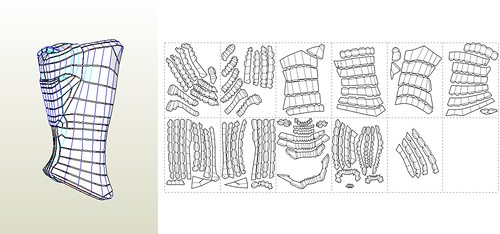
Dragonbone Greave in Pepakura by vrogy, on Flickr
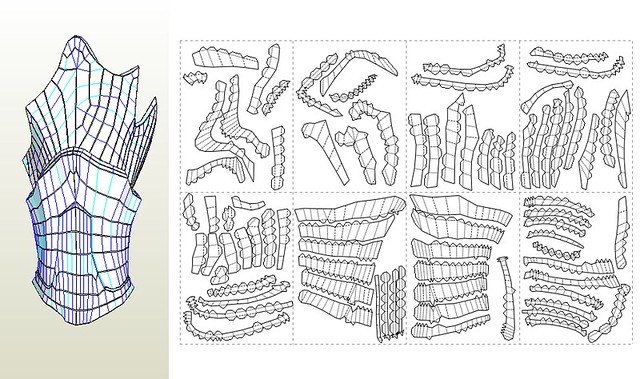
Dragonbone Forearm in Pepakura by vrogy, on Flickr
need to finish models and unfolds, cut, and assemble.